zai skis studio visit & interview with creative officer, simon jacomet
image courtesy of zai
founded in 2003 by designer and now chief creative officer simon jacomet, the swiss ski brand, zai, produce handcrafted skis from a range of fine materials, that provide uncompromising performance. the company manufacture these products, as well as fitting snow sport accessories, to suit beginners through to olympic champions. following our previous interview with simon, designboom traveled to zai’s studio in disentis, switzerland, to learn more about the design and hand-craftsmanship of their high-end skis.
image © designboom
stepping inside from the snow-covered slopes of the swiss alps, zai’s entrance to their creative workshop showcases their radical ski designs, apparel and golf putters. walking past these proudly displayed products and into the factory, simon began to explain the precise stages for creating the high-end skis. straightaway it became apparent at how much care and how much knowledge could be expressed through hand-production, when compared to mass-manufacturing. he explained how the use of extraordinary materials, which at first caused others to laugh and question their ideas, could be introduced to provide capabilities unlike anything else. in the same sense of uniqueness, the hand-crafting of the materials enable them to work it how they and the clients want, and to continuously produce skis which are individual.
if a material doesn’t add an element to a ski’s ability, then it won’t be used. this is the strict criteria that zai enforces, but it is no wonder, due to the high-costs of the materials that are available in large or low quantities. another factor is that they need to fit the brand’s DNA, so durability and appearance is considered as important as its performance properties.
view inside zai’s factory and at their machinery
image © designboom
in addition to this, crafting the skis from hand allows zai to fabricate them unlike anyone or any other company can. grinding away to what people need rather than the bare minimum, their equipment feature a 1.7mm base – the thickest on market – and ensures quality as well as durability. sticking with this factor and how they compound different materials to a ski, for example when they feature stainless steel top edges, their products lose 5% tensions after 100 days of use, compared to 25% over 30 days for mass-produced ones.
a metal template of ski
image © designboom
their designs always relate back to performance. the odd shapes, highlighted perfectly by the double-tip ‘laisa’, are created for specific reasons and to provide a necessary function. simon was keen to stress how zai do not pay any attention to trends, but do strive on creating striking, attractive, and symmetrical forms. using the natural colors of the materials, except when implementing rubber, components showcase this and the raw passion of the brand. he even mentioned how he proposed the notion of removing the zai logo when creating new products, but their salesman was not happy about this. the idea is interesting though, as it would ensure that the developments would feel, perform and look like a zai, before any branding was introduced.
an example of the variety of materials they use
image courtesy of zai
after building a unique reputation by crafting sports equipment from a wide range of materials such as carbon fiber, stone, walnut and felt, zai are continuously pushing the possibilities and capabilities of ski design. after the studio tour, we talked with simon to delve deeper into the brand, and discussed topics such as; what truly makes zai stand out above competitors, why they use such unusual components and how the performance factor is always a product’s driving force in development.
finishing the ‘laisa’
image courtesy of zai
manufacturing by hand ensures the skis are created with great care and detail
image courtesy of zai
DB: what makes zai skis different to those of other high end companies?
SJ: our philosophy is to try and give our clients as many different reasons to buy the product as possible. however, different clients look for different reasons to buy the product, as for one person it is important to have a fast ski, whereas for another, its all about durability. a key element may also be about design or uniqueness, so when we develop a product, we come from multiple directions. the main importance for us however, is of course, the driving performance because skis are designed to ski. I am always searching for the driving performance which meets the philosophy of zai – effortless skiing, enjoyable skiing and to offer the possibility to exceed existing limits. in the end it’s about creating a tool that enables the user to do what we describe in our company guideline – a poem: ‘zai finds the line reading the mountain plays in the snow like jackdaws in the sky.’
simon jacomet working on the leather collaboration with bally
image courtesy of zai
DB: what are the key factors for designing the skis and developing new concepts?
SJ: there are many different ways of approaching it and due to the experience of doing so for over 10 years, it is often mixed up. we usually start with the driving performance but then I start to vary single materials or add a new one. all together, this method brings up original ideas, where sometimes you start with new materials, without knowing what the properties are, and out of this you can develop something unexpected. other times, we analyze a certain performance factor of the ski and want to enhance it, so instead we work in more detail to build upon the existing knowledge. I think whats also important, is to be very open minded but to know very well about what has already been done. developing skis has a complexity which can not yet be simulated virtually, there are endless factors to be understood and controlled.
polishing the skis
image courtesy of zai
DB: how do zai skis balance the importance between performance and the appearance of the products?
SJ: the balance is quite radical as without the performance we wouldn’t sell skis. we have had quite radical looking skis in the past, which didn’t have the performance factor so never made it to the market. this is really the first and the hardest step within the whole process. once the performance requirements are met during the transition from prototyping to the serial production, the design begins to count for even more. however, without the existing performance we don’t take a product forward.
crafting the walnut wood ‘testa’
image courtesy of zai
DB: could you outline some of the key materials that you use and stress how important the difference between the materials are for each product?
SJ: we use different materials to provide or reduce certain elements. for example, when wanting to lower the weight, the best way is to work with carbon fibers. they have amazing properties for tension and for reducing weight, but influence the ski’s performance in a wrong direction. to resolve this, we combine it with other composite materials to get the desired driving performance or character that we are looking for. another point which is very important for us, is the surface of the ski. we say that the material we use there, already needs to have a certain function and needs to have an influence on the driving performance. as well, it needs to be re-workable and if possible, to have a certain uniqueness. this is always the best as just one function or one reason is not enough for a material to be applied.
the tips of the ‘testa’ skis
image courtesy of zai
DB: what is your favorite material to work with for manufacturing and for the capabilities of performance?
SJ: my favorite materials are always the ones I didn’t understand at first, or the ones that I am currently working on because then they are the most challenging. one which is still absolutely amazing is the stone we use, and just understanding how we can take this technology further. I will never lose the interest in the stone, but this the same for all the skis in the selection. I would not say that I have a favorite ski because they have all been designed for certain purposes. as I always say, the most interesting, is the one I am working on.
what I also like about the materials we use, is its diversity because we sometimes work with stone and then with another material like felt – which are completely different to each other. I think by making experiences with certain materials, you start to understand their different properties – from soft to hard, from stiff to smooth. all together this brings your knowledge forward, but the genuine secrets are in the way of combining them.
zai’s 2014/2015 collection
image courtesy of zai
DB: what is the hardest stage of the design and manufacturing of the skis?
SJ: as mentioned before, the hardest stage is the development from prototype to serial production. nowadays, people talk a lot about innovation, but in the end, innovation means to make the whole development and to sell a product. if you are not able to sell it, then it doesn’t count as innovation. with 10 years of experience, the starting point becomes easier because there are different ways of experiencing and different routes of getting there. at the beginning, my knowledge about different materials was not so big and whats very interesting is that, after I worked on certain materials where I didn’t succeed, I eventually found ways of doing so. there were several materials where I was told to forget it, its impossible, and because I was told so, I’ve never forgotten them. later and after gaining more experience, I have been able to implement and apply them to our products.
DB: could you tell us about the new range that’s been developed? are there anything we should look forward to seeing?
SJ: in time for next winter, we just presented the new range of skis which mainly focuses on the spada collection – the ones with the stone core – and how I was able to apply a certain surface, that I have been wanting to use for over 8 years. its a celloluse and fulfills all the elements as well as the DNA needed for a zai ski. I am happy that I have successfully applied it and that it influences the driving performance in a way I was hoping it would. it makes the product even more smooth and more simple to ski with, but at the same time, also allows the users to challenge themselves. the product always makes you feel on the safe side and let you explore without stopping.
a close look at the ‘scadin’ product
image © designboom
DB: continuing from your previous collaborations with hublot and bentley, are they any new partnerships in the works or if not, are there any companies that you would really like for zai to collaborate with?
SJ: I think there are plenty of companies which share our values. we consider this but also keep in mind that, as a brand it is important not to change your partners often. for example, we have already made good experiences with bentley, and have had different car companies contact us to propose a partnership. obviously, we say no because we decided to work with bentley, but also because we still feel that there are more possibilities to do together. as a brand, I think you need to take care not to partner up with too many companies, otherwise the clients will not understand your product anymore. this is what we care most about and we also need to see a reason to partner up. there are quite a lot of reasons, often its the similar philosophy, but for us, as a small brand on the market, it also helps to make us more known through a partnership.
the studio steps out onto the snow-covered swiss alps
image © designboom
DB: what made you step into the golf field?
SJ: there are two different reasons to step into the golf field. one, we wanted to transfer the experiences we made with certain materials into golf, because we are convinced that they work there. there are many similarities between skiing and golf, for example, in terms of moment of inertia, center of gravity, and about tempting. these are elements we are working quite a lot on for the skis, so therefore it was, in a certain way, obvious for us. the other reason is because skiing is a winter business so we wanted to spread our work over the whole year.
DB: are there more plans to develop the golf products further?
SJ: yes, in golf what we also had to understand and except is that we couldn’t just step from a ski brand to golf. by stepping into golf, it meant we needed to build up like a new brand, even though some people know us for our ski business. in the end, this requires a lot of time and a lot of steps.
the sabi putter
image courtesy of zai
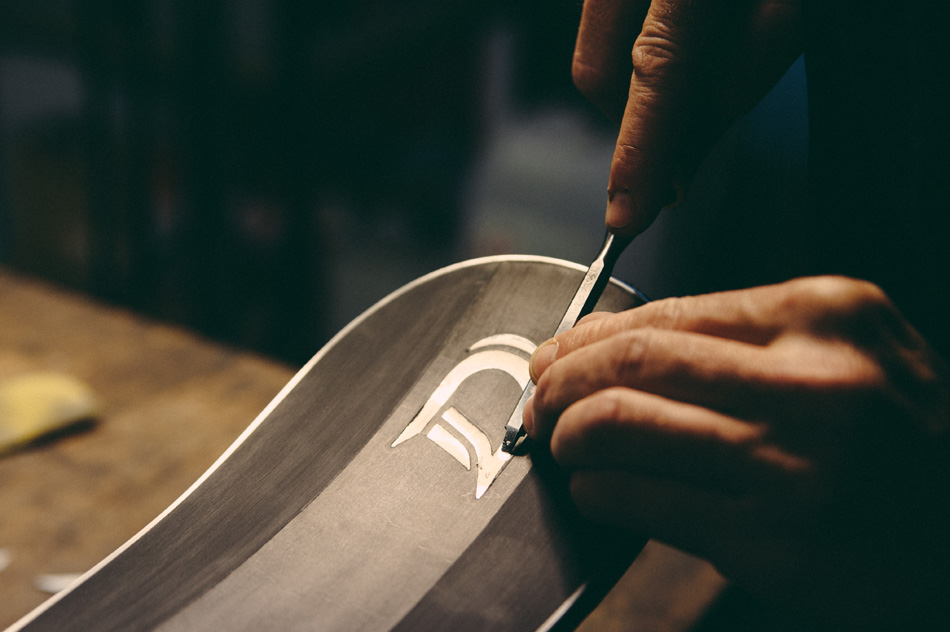
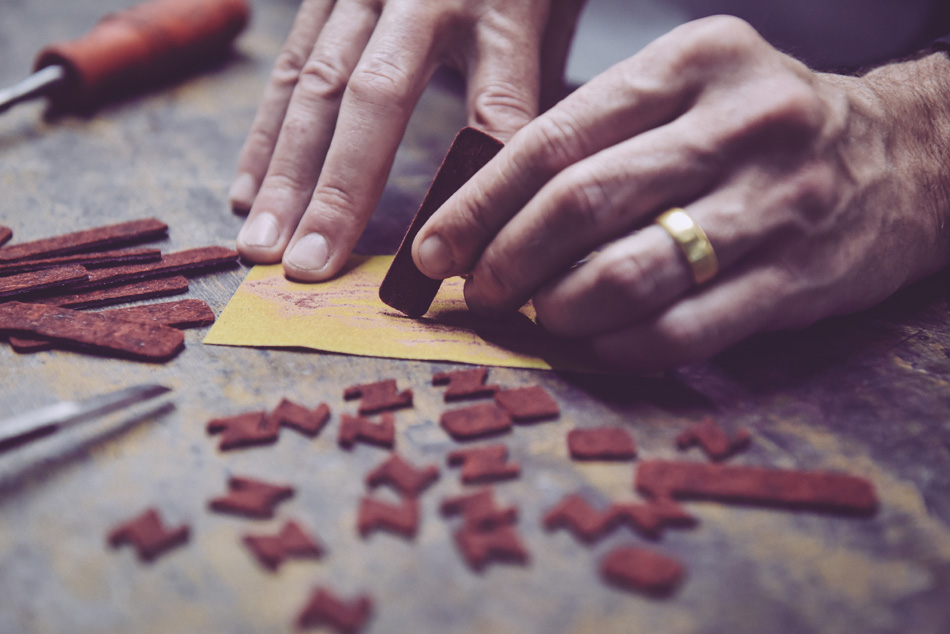
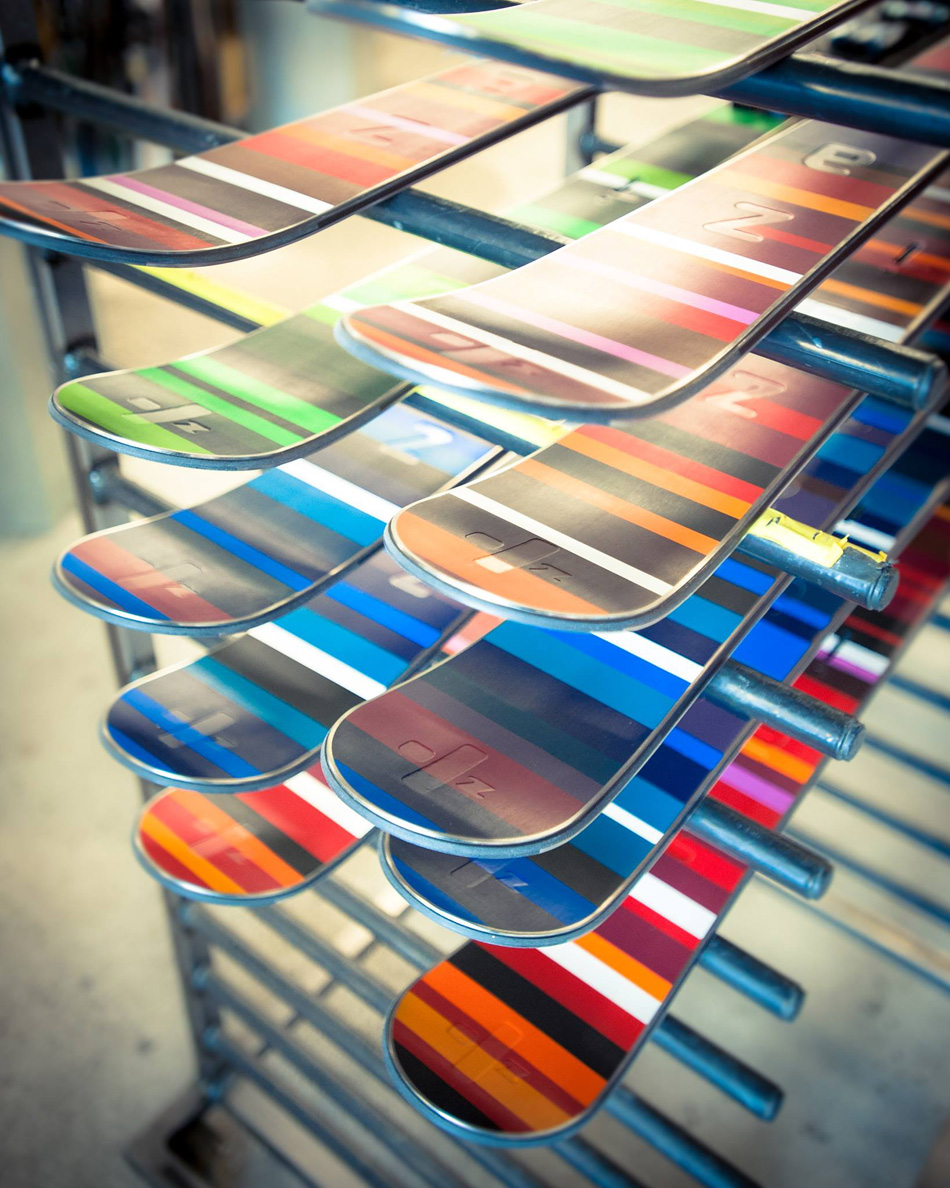
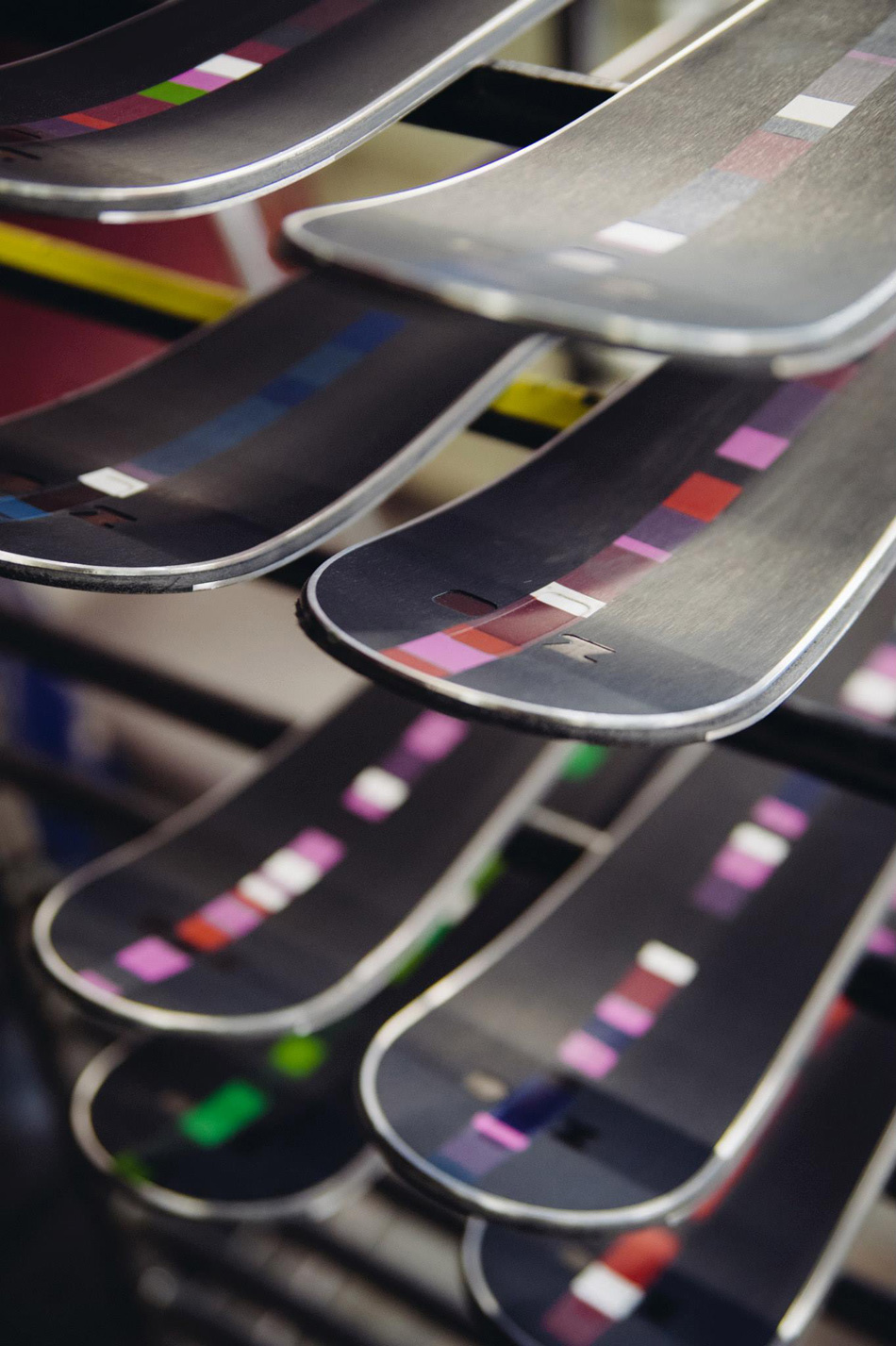
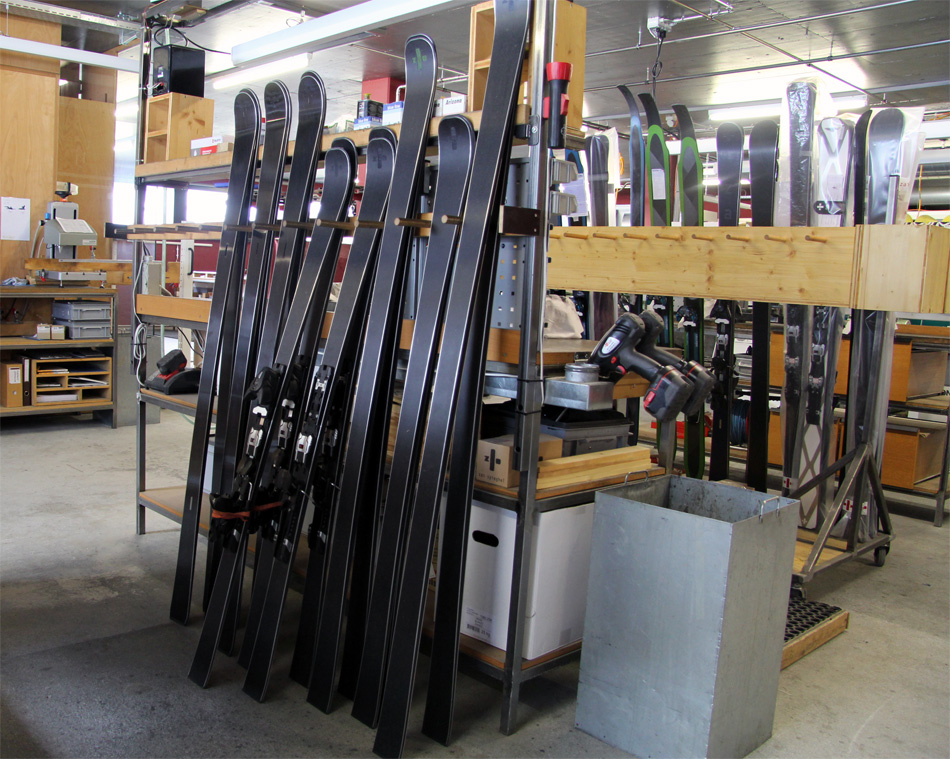

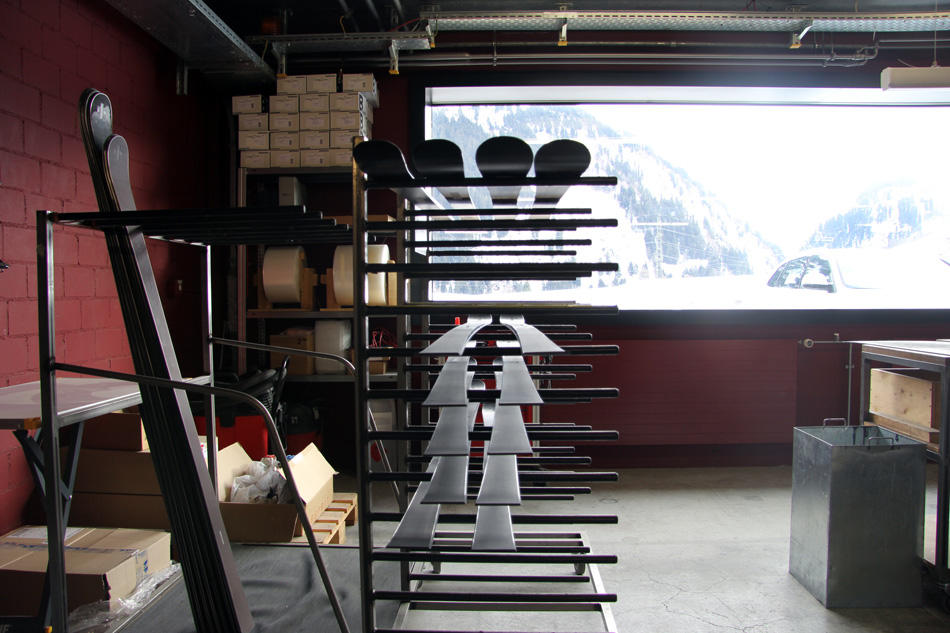
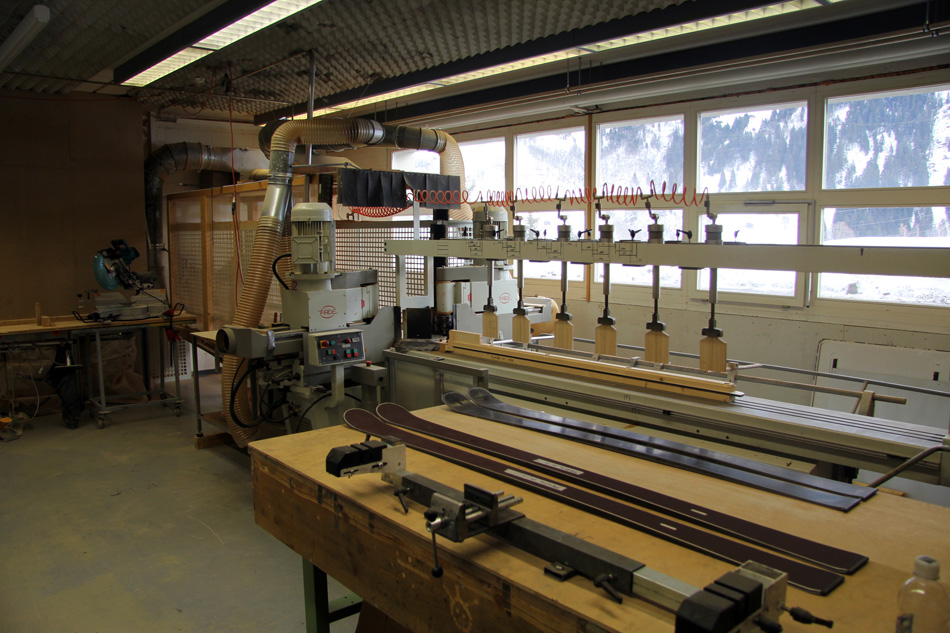
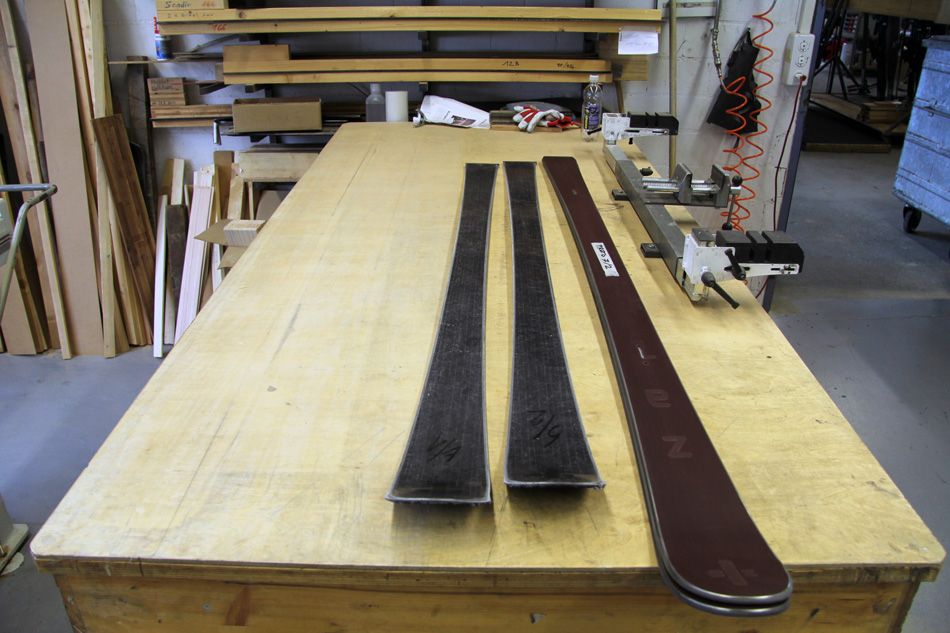
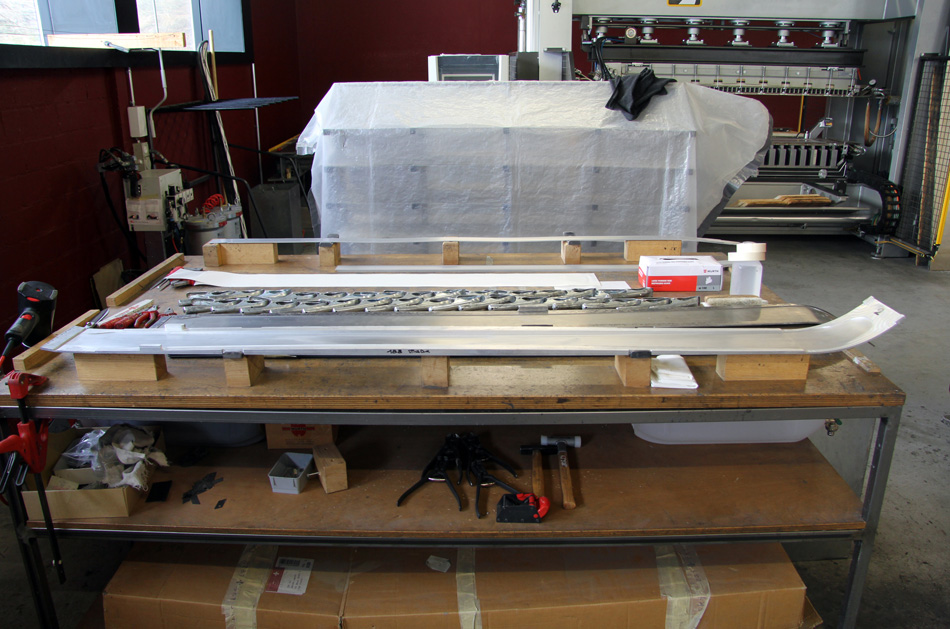
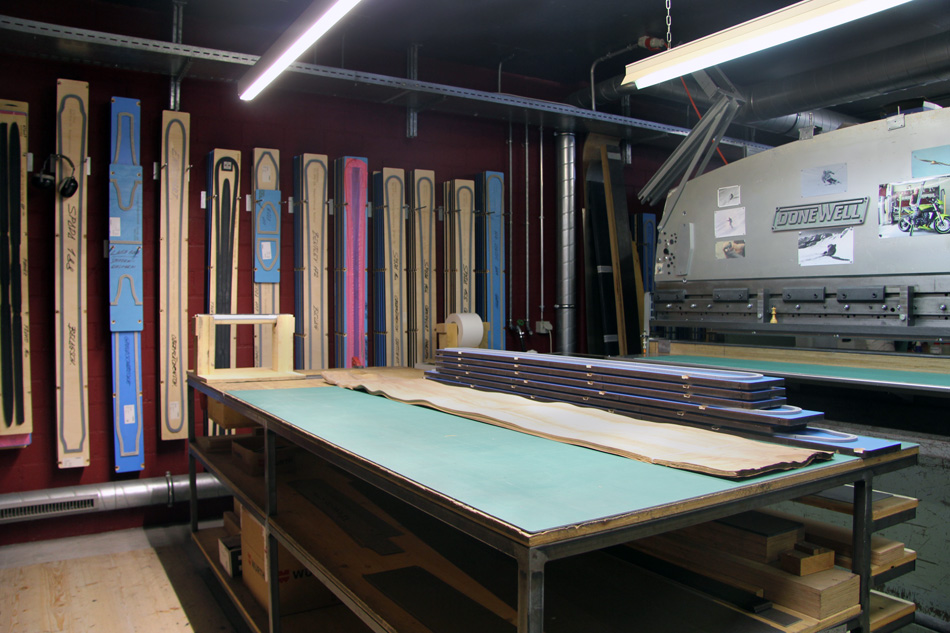
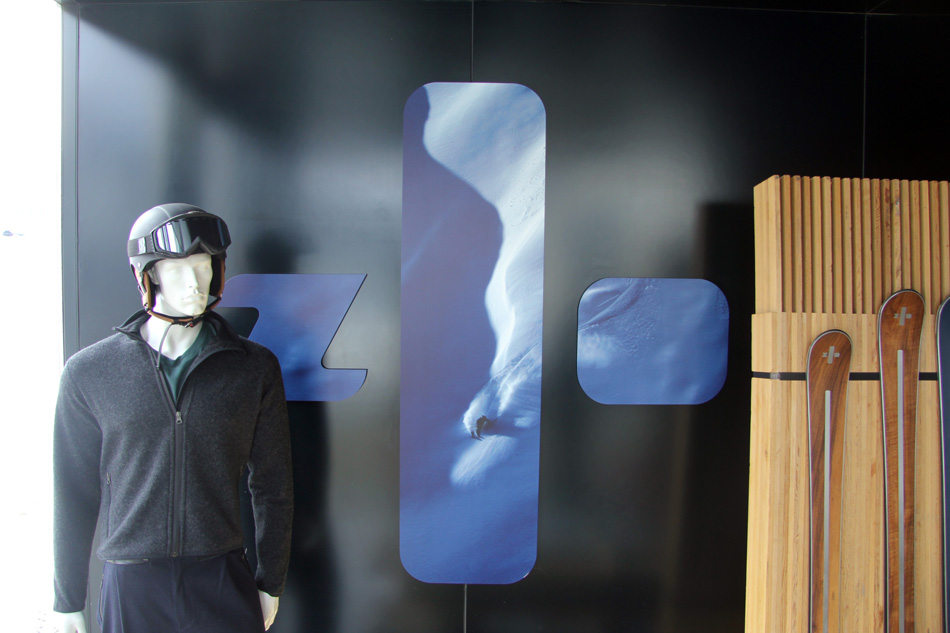
happening now! in an exclusive interview with designbooom, CMP design studio reveals the backstory of woven chair griante — a collection that celebrates twenty years of Pedrali’s establishment of its wooden division.