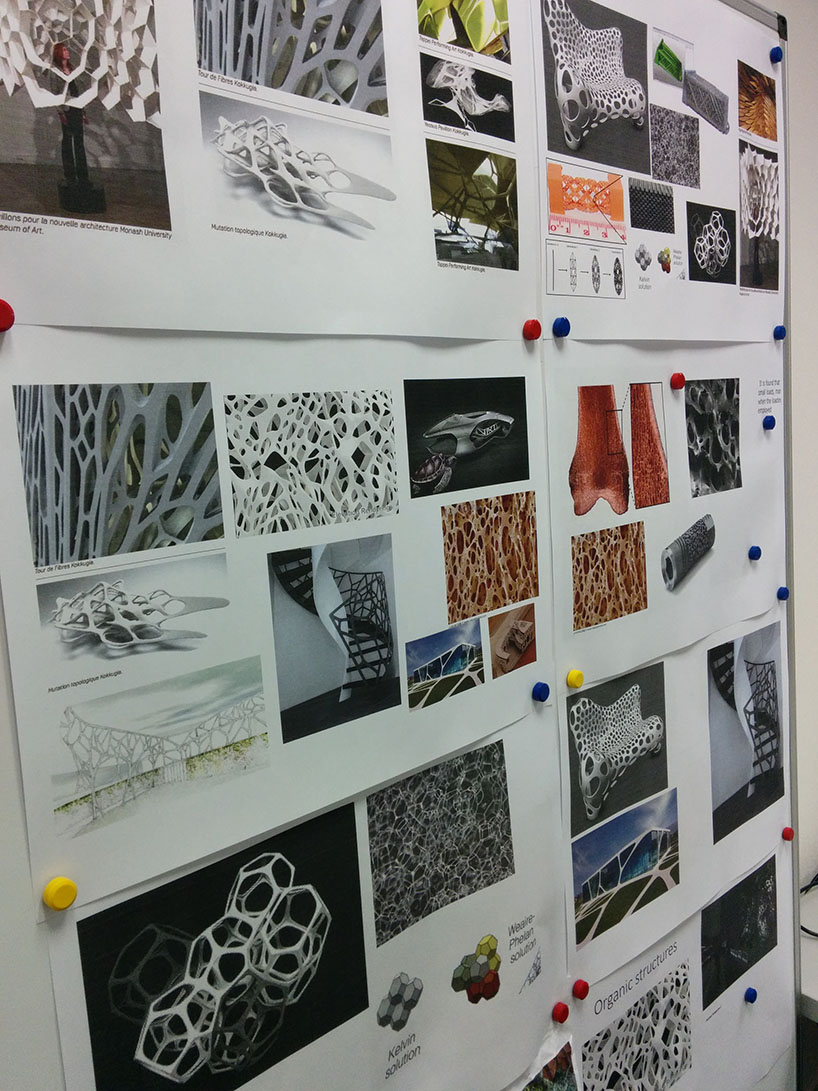
Omega snowboard binding by MA Vivant from france
designer's own words:
I am a young product design engineer fond of new manufacturing options and materials. I also am an avid snowboarder, and one thing I am always dreading while snowboarding is how heavy my gear feels at the end of the day and how I can imagine making it lighter and more performing.
I got exposed to 3D printing early in my studies and have followed with great interest its expansion in the last couple of years. I was excited when so many subcontractors started equipping their shops and factories with metal sintering printers that could break the barriers and restrictions of die casting, molding and forging.
So why not have a 3D printed snowboard binding? Of course in today’s market, the visualized product would be very pricey and considered as a luxurious item. But why not imagine affordable printed parts for the average consumer in a few years? And of course the luxury market is always there for top of the shelf products and concepts.
In the race to weight reduction 3D printers have a lot to bring. Bone structures are one of the lightest and most resistant ever studied, so transferring this lattice structure into the product made sense. But I didn’t want it to look like a 3D printer demonstration object. The 3D printed sidewalls of the binding seem minimal and fine, simple from afar, a second read of the object reveals the lattice structure trapped between the two walls that form the sidewall. The shape comprises both angular and organic forms to contrast with natural and man-made structures. The sidewalls are to be manufactured in titanium with an anodized dual finish by the means of selective films. Depending on the lattice structure geometry, laser or electron beam sintering should be preferred. To achieve optimal design and minimum weight, I conducted a pre study using new material optimization softwares (here Solidthinking by Altair).
The rest of the binding is optimized as well. The highback (back support part) is designed in a mix of carbon and fiberglass layers. It is lightweight and responsive with a ribbed surface unusual in this industry. To allow for small radius on the rib shapes, several small sheets of carbon are to be used for molding instead of one main sheet. This will prevent fiber distortions and allow the sheets to settle into place with molding pressure. The highback strengthens the severe and technical look of the angulated sidewall parts.
Finally the straps are here designed for women with organic shapes and a ballerina-like design overlapping a random oval pattern. The anchor zones for the buckles are molded in rigid TPU and the rest of the strap is overmolded with a softer version of the polymer for comfort. The inside of the strap comprises a cushioned texture for visual comfort. This organic shape supports the organic sections of the sidewall. The molded strap is 3D fitted to the ankle and no more fabric tearing or broken stitching.
This is a one of a kind snowboard binding for riders who want the best riding response at the lowest weight.
Project Mood Board
Material optimization study (Solidthinking)
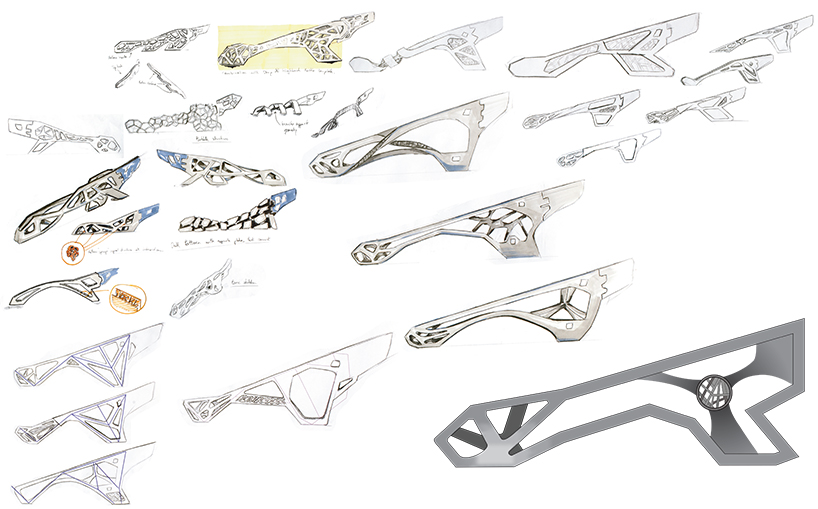
Design Study sidewalls
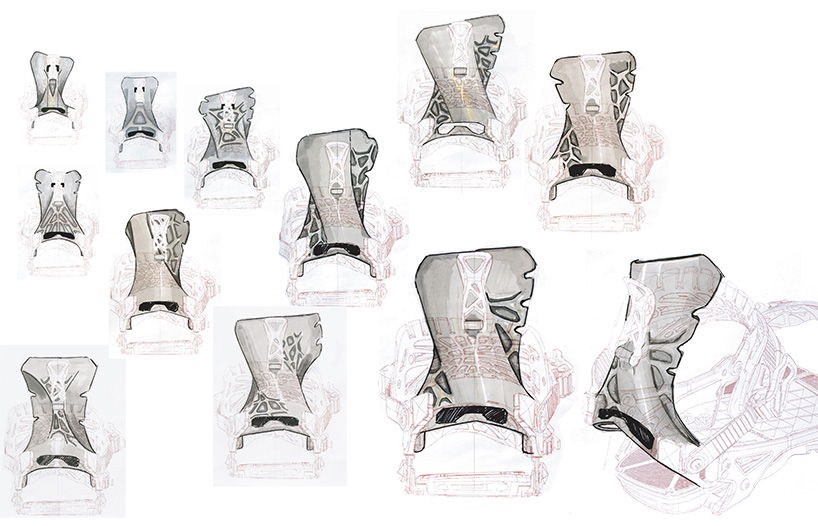
Design study highback
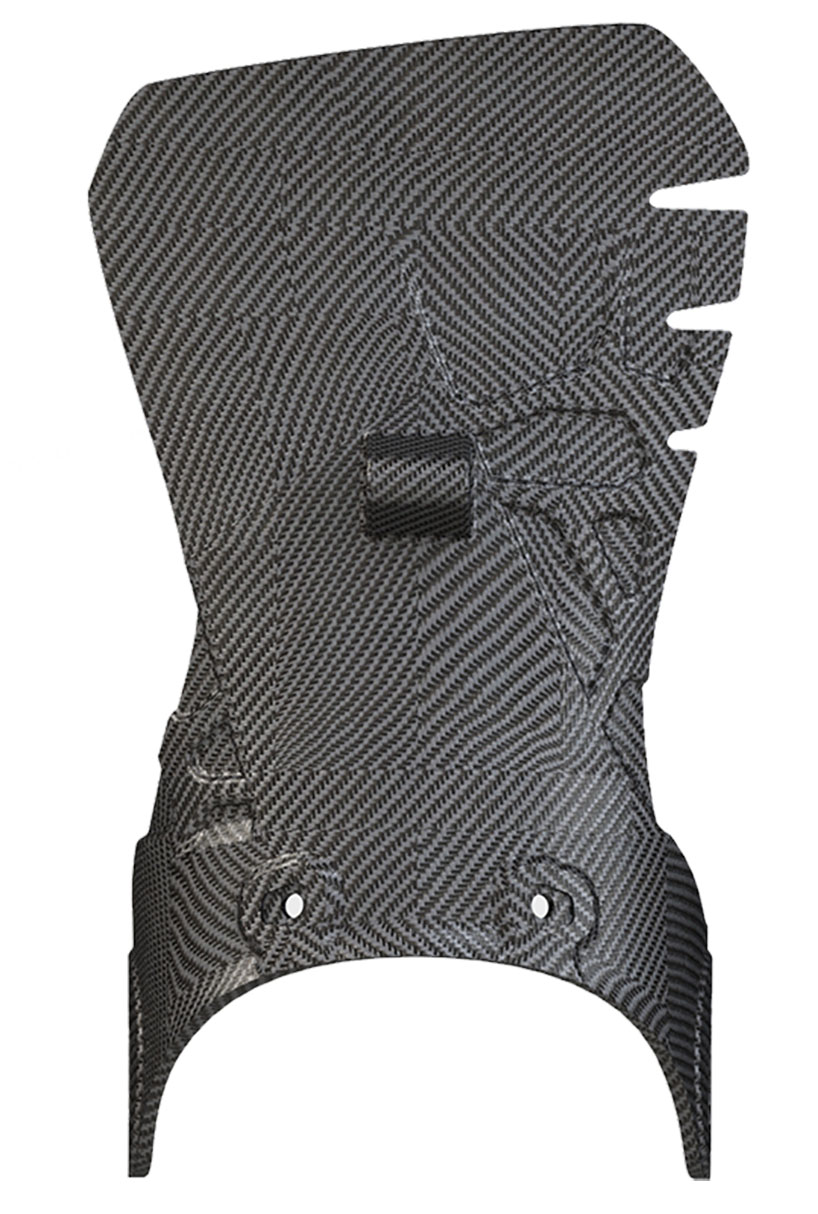
Carbon highback
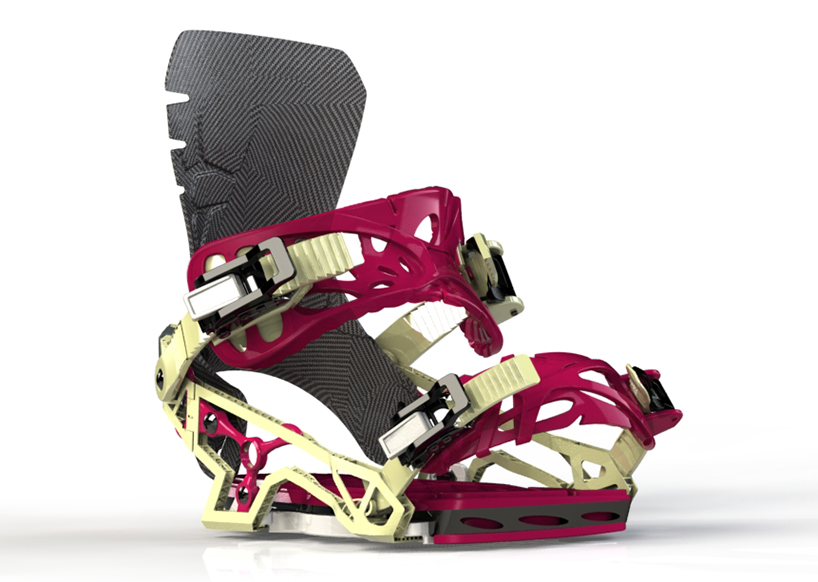
Omega women snowboard biunding=