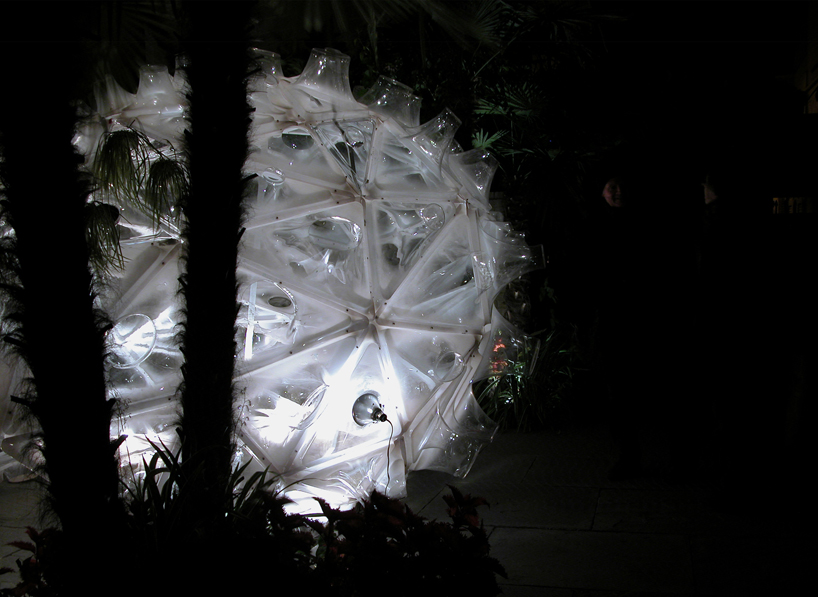
adaptation by Gernot Riether from usa
designer's own words:
the adaptation pavilion was designed as an efficient lightweight shell structure that allows for easy transportation and rapid assembly and disassembly. the base geometry of a sphere was transformed to adapt to specific site conditions and solar orientation. it was optimized relative to size and location of apertures, floor surface, program and structure. the geometry was then tessellated into 320 unique triangular proto-cells that were transformed into cells of different attributes. depending on its position the edges of each cell were folded differently to provide stiffness within the cell and to make up the overall structure. each cell adapted further to different functions: windows; seating; foundation; brackets for an electrical lighting system; a day lighting system; containers for plants; and water collectors. the process of informing and transforming each proto-cell based on specific functions was entirely scripted. each function therefore had to be articulated as rules that informed the cells geometric transformations. the degree of unpredictability in form increased with the number of sets of information that operated on the same geometry. scripting became the primer design tool and was not just to automate an existing design. the final overall form and spatial qualities of the pavilion in turn emerged from the cells variations. scripting the entire pavilion in this manner dramatically increased continuity between digital design and fabrication. engraved instructions that helped to connect the different cells, numbers of all edges and details that changed with each cell could be added easily to the script as additional information.
the cells were made of petgs (glycol-modified polyethylene terephthalate). the highly malleable nature of this material made it suitable to the digitally derived form of the pavilion and its complex geometry and cell variations. the material is light, impact resistant and easy to fabricate. this contributed to rapid assembly, disassembly and transportation. the material choice also responded to sustainability and environmental concerns. it can be produced from recycled plastic and can after its use be recycled further. it is also a material that is specific to the site and region. petg can be produced from sugarcane, a plant that has been an integral part of the culture and economy of louisiana for 200 years. the material is manufactured from sugar cane feedstock that is used to produce ethanol, which after a dehydration process becomes ethylene. producing petg from sugarcane has tremendous environmental benefits that might make plastic the building material of the 21st century. any plant produces oxygen and extracts carbon dioxide from the atmosphere. according to dow chemical, one of the largest manufacturers of petg, each pound of plastic produced represents a total gain of two pounds co2 removed from the atmosphere. since the aia pavilion used 272 pounds of material, the production of the pavilion would remove 544 pounds of co2 from the atmosphere.
the various triangular outlines of the individual modules were routed from petg sheets. each of the triangles was then thermoformed into a three dimensional shape. to save material a single flexible mold was developed that could be modified easily to produce different shapes from different triangles. thermoforming, a technique used mostly in the packaging industry, was used to generate the final geometries of the cells. this technique involved fewer parts and tooling than other molding techniques, which allowed for cost and time effective production. it was also very precise, resulting in very small assembly tolerances.
using a minimum amount of material to produce the pavilion the flexible mold was constructed from a digitally fabricated kit of parts. its main components were a flexible frame and stamp. the frame held the material in place during the forming process. the stamp transformed each cell into different shapes. the mold combined three different thermoforming techniques: drape forming, vacuum forming and draping. rearranging the few elements of the flexible mold was used to produce the 320 different building cells of the pavilion but could be further used to produce an infinite number of other variations. all cells were prefabricated and assembled into 6 larger components designed to stack and fit compactly into a small truck for transport.
the pavilion as a glowing object at night
interior at night
exterior view
detail of the pavilion’s structural skin
shifting triangle segments were part of the flexible mold
the geometry of each cell emerged from competing sets of information