nendo forms semi-wrinkle washi lamp using 3D paper moulding
all photos by hiroshi iwasaki
the process of making washi paper involves passing fine screens through a bath of plant pulp and water, collecting and draining the substance, drying it, and peeling it off in sheets. but, taniguchi aoya washi, a company in tottori prefecture in western japan, has taken the traditional technique and modified it to create seamless three-dimensional washi forms; and they have done so in such a way that the resulting pieces are often confused with being that of white glass or plastic. they add devil’s tongue (konnyaku) in order to generate wrinkles that emphasize the particular characteristics of the fibrous material, however at the same time, concealing the fact that the designs are made using the long-established practice.
floor or table version
so, when asked to develop a product that promoted the craftsmanship of taniguchi aoya washi, nendo decided to produce a series of lights which would bring out the best of both worlds. the resulting ‘semi-washi lamps’ as the name implies, are that only half-formed using the wrinkling process, so that the two different effects come together. in nendo’s modified method, the creases shrink the fixtures overall size–the studio calculated in reverse, from the final desired dimensions, in order to determine the initial proportions. thus, the ‘semi-washi lamps’ project an aesthetic that combines softness and tensility, that only three-dimensional washi can exhibit. the lights are exclusively available at seibu department stores in japan.
up close of the wrinkles
pendant version
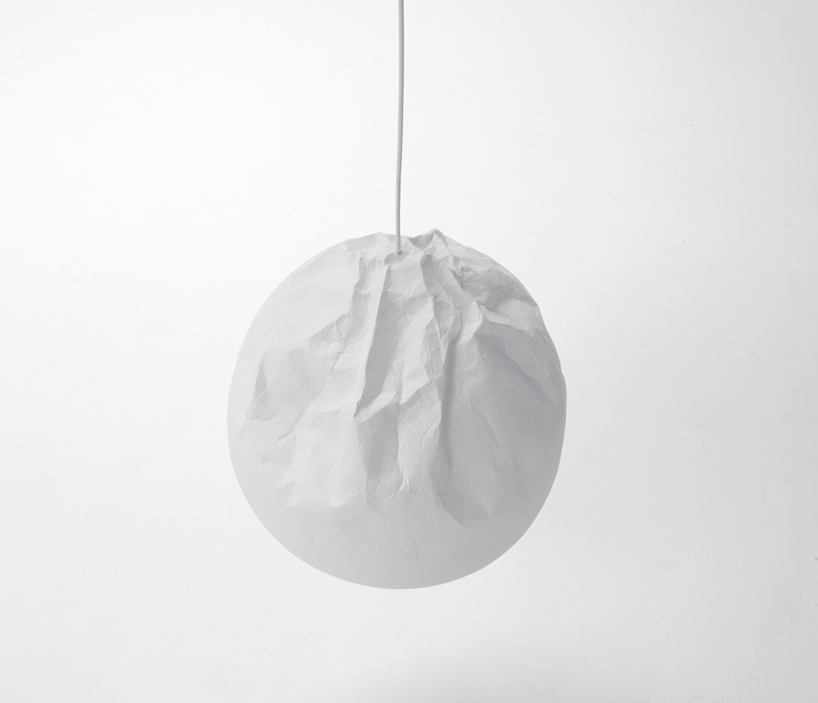
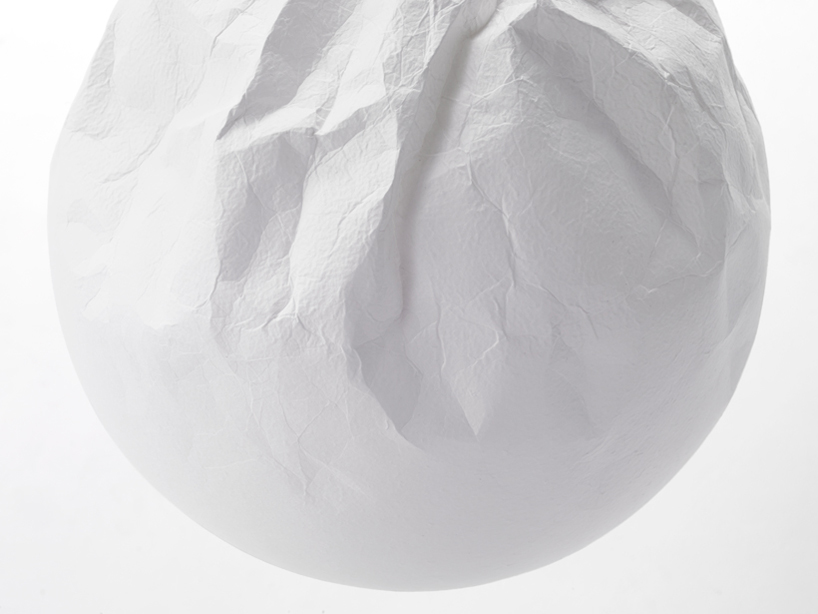
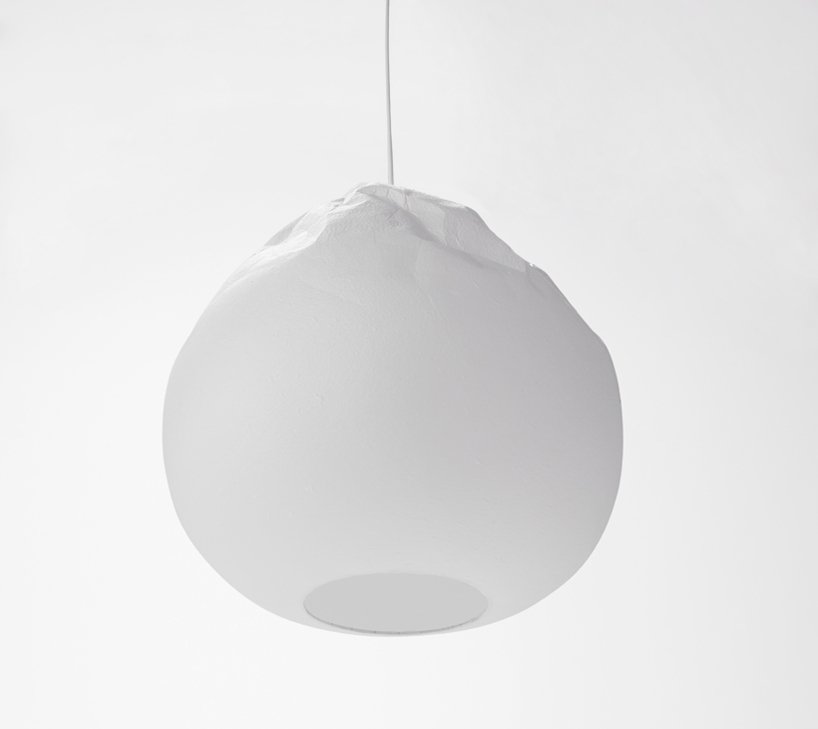
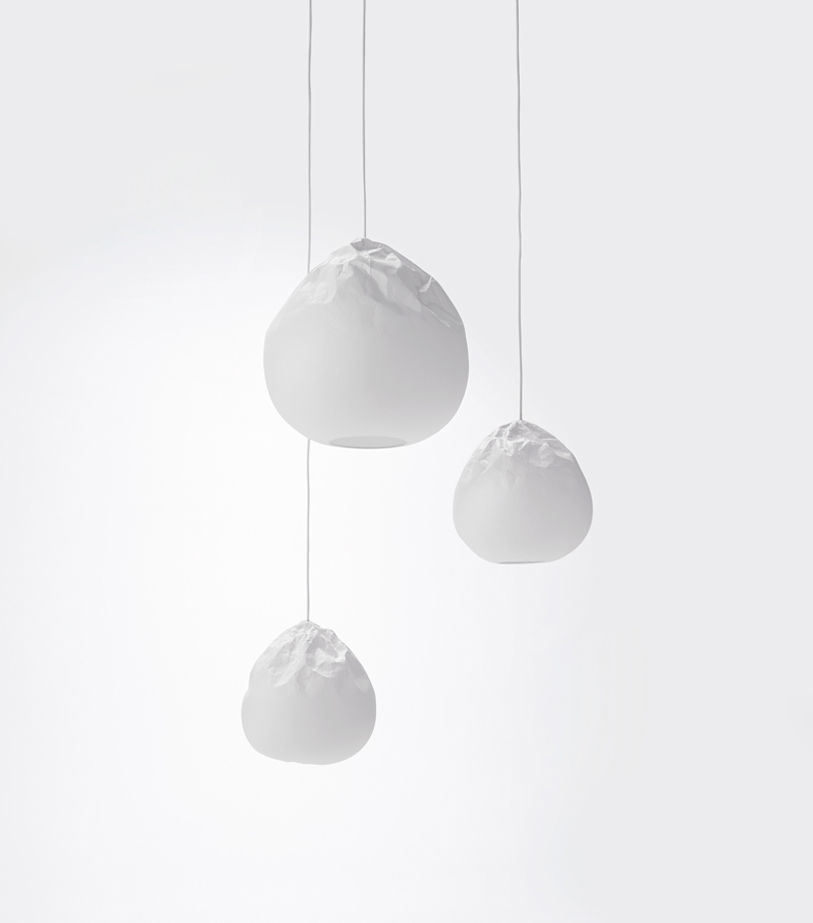
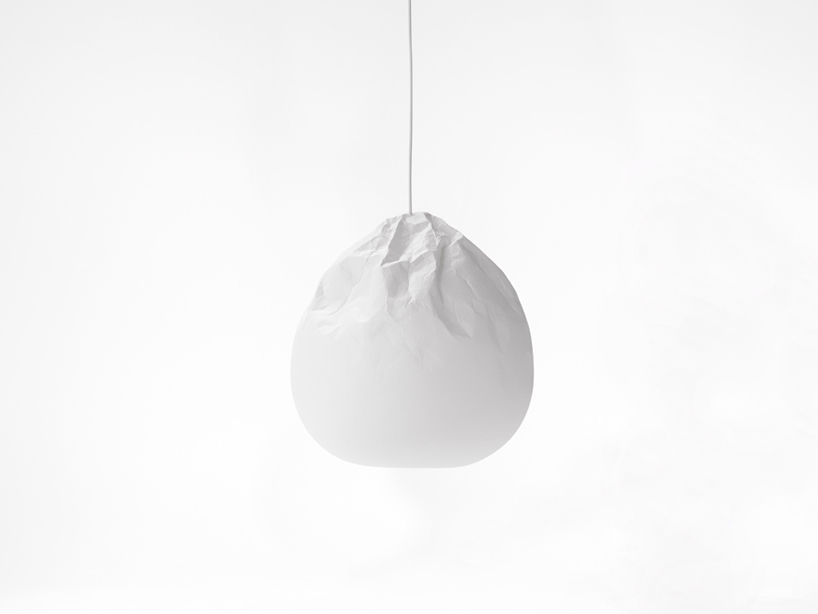
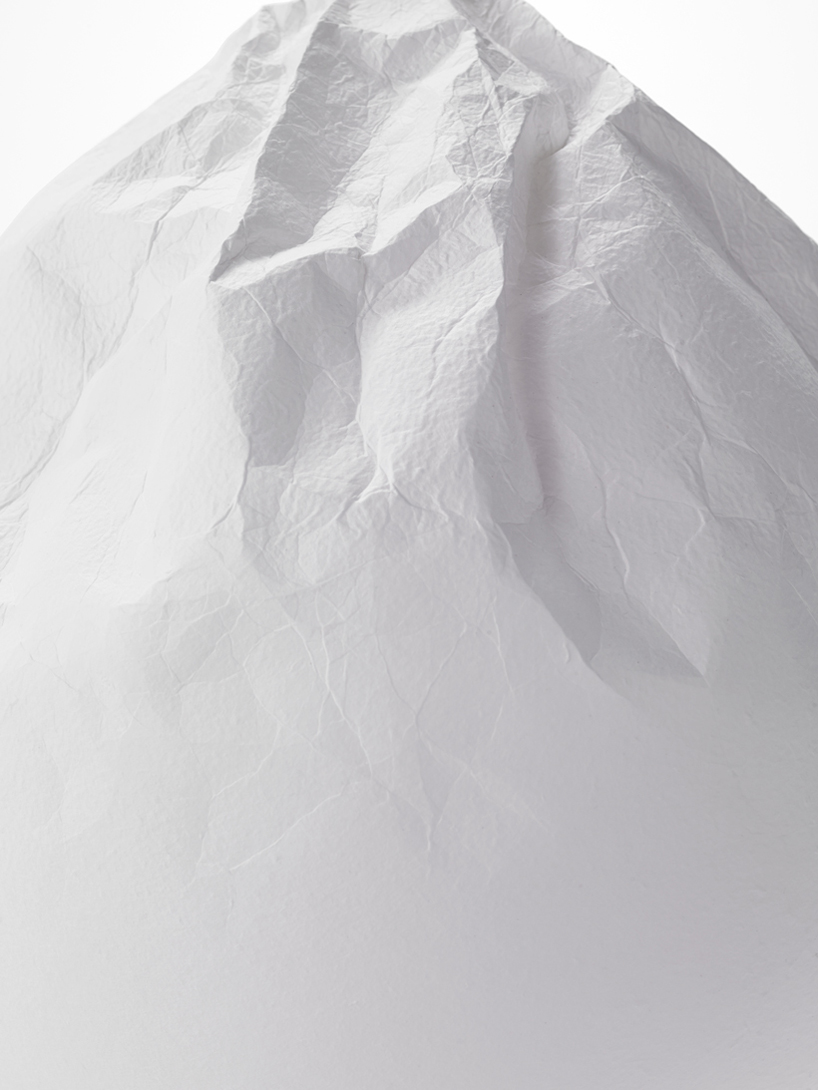
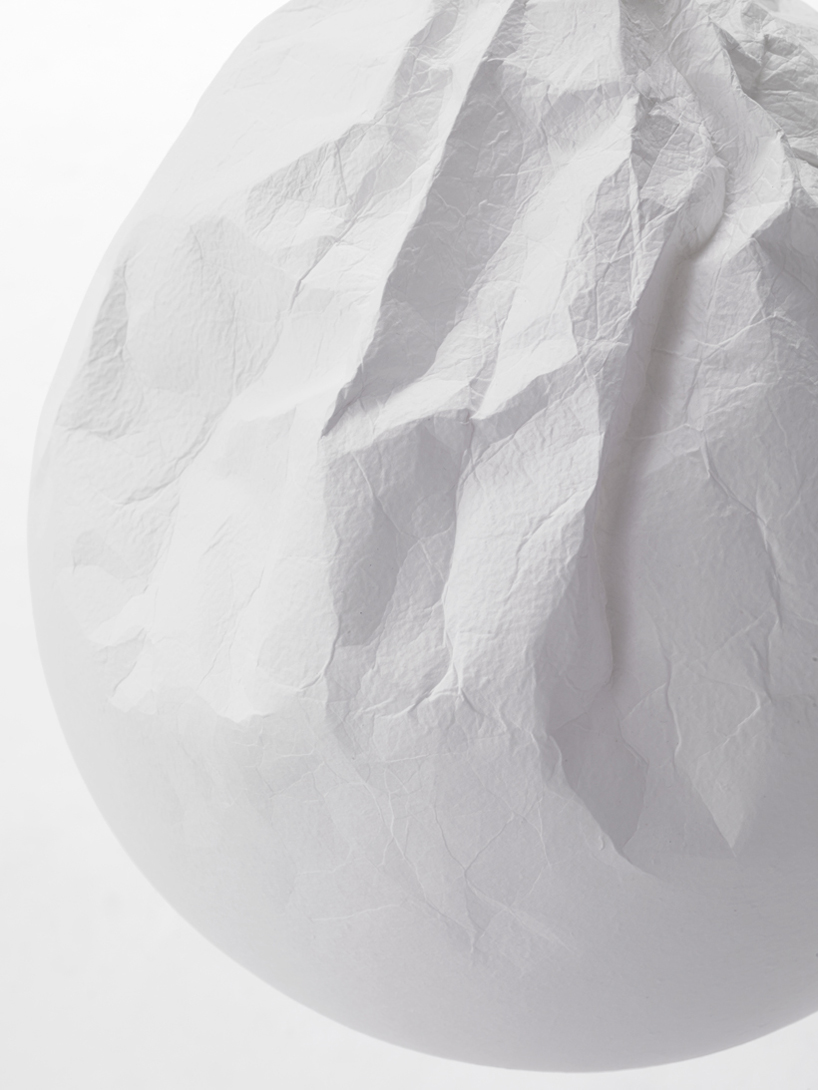
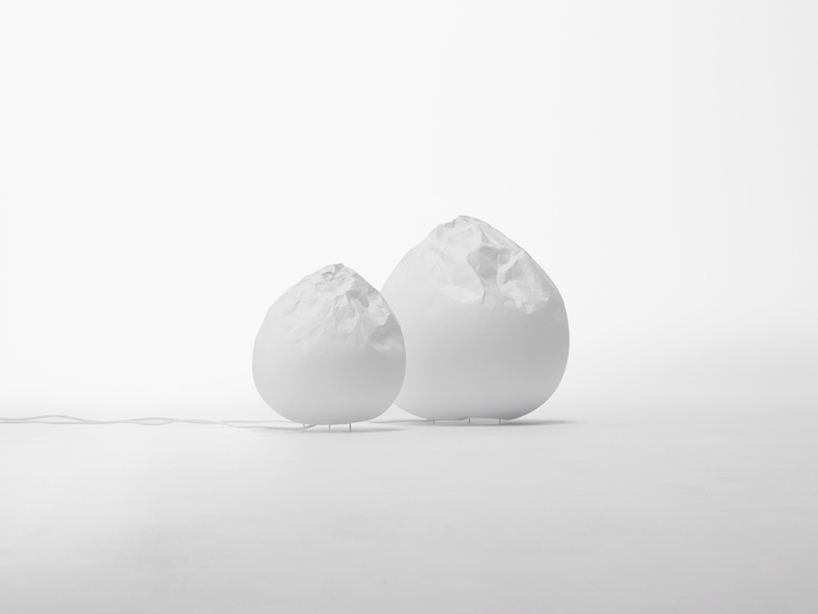