maxime loiseau forms super-thin headphones with printed electronics
all images courtesy of maxime loiseau
‘roll to roll’ production processes are often applied to the miniaturization of technologies, in techniques like printed electronic circuits, hot welding, embossing or laser cutting — in effect, simplifying the composition of an electronic device. presented at wanted design for the ENSCI — diplorama+ exhibition during new york design week 2015, maxime loiseau explored this type of manufacturing method to smarten and streamline a ubiquitous technology: headphones.
‘through an object, I challenge this new way of designing and producing an object’, loiseau describes. ‘I question the advantages and benefits of ‘roll to roll’ production techniques, and also explore how those techniques influences the formal vocabulary of the object, made of thin strata and superposed layers.’
the model’s bluetooth headphones adopt printed lithium/ion battery and printed photovoltaics cell technology
in terms of production and materials, everything has been simplified: electronic circuits are printed instead of using wires, plastics are welded instead of using junction parts, and shape is given through embossing rather than expensive injection molds. aesthetically, as the process is similar to that of offset printing system, then object conception become similar to a graphic composition and each technical component becomes legible again — for example, you can see the circuit feeding the piezoelectric cell.
electronic cells are printed on the outside of the headphones, forming a pattern layer overlaying the others
the speaker functions based on the vibration of a piezoelectric cell, where electricity results from pressure. through the piezoelectricity that occurs on the plastic surface, the system produces a sound comparable to a conventional unit, but is only 1mm thick.
the ‘roll to roll’ design adopts simplified elements and efficient processes, where technology is the material itself, rather than an assemblage of various matter. the headphones can be made with one single production line without injection molding — a reflection on the economy of processes, materials and means in electronic devices production. each earpiece can be composed of 8 simple parts, whereas a standard headphone can use up to 50 pieces.
the ‘roll to roll’ design adopts simplified elements and efficient processes
‘the project doesn’t change the way we will use headphones’, loiseau says. ‘the purpose here is to offer a reflection about producing electronic devices in a smarter way. the more materials are advanced, the more they are paradoxically easy to work. through one production process, we can then using less process, less material, energy and pieces. at the same time, I tried to use the possibilities of the process to create an aesthetic result from it, a more fair product, with no superfluous parts.’
the earpieces comprise a rigid frame for the speaker, and are surrounded by a steel piece
this model has only one-side cable with printed electronics that powering each of the speakers
the speaker functions based on the vibration of a piezoelectric cell
the back of the earpiece is engraved to emphasize the shape and create different shades of black
by hot welding the cable, the electrical circuit contained is brought into contact with circuits in the speaker
the junction of the flat cable is intentionally highlighted to reveal its thinness
simplicity is revealed in the design and composition of the object
‘roll to roll’ headphones research
video courtesy of maxime loiseau
all parts and process in the traditional making of headphones has been simplified
research for earpiece, hoop, cable, and process
functional prototype of speakers using a classic piezoelectric cell
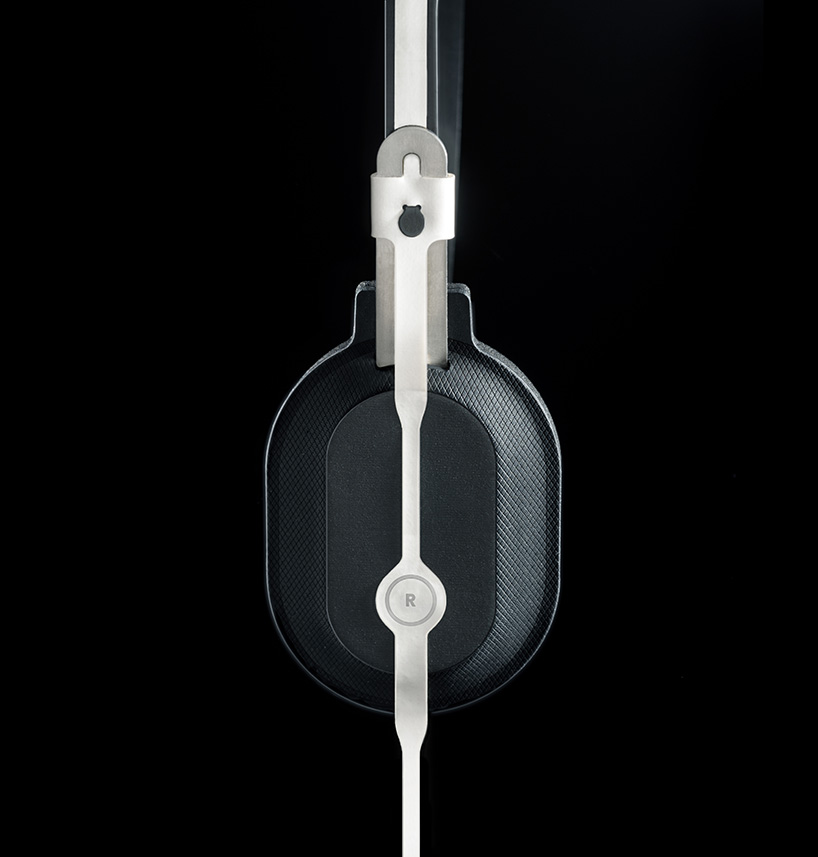
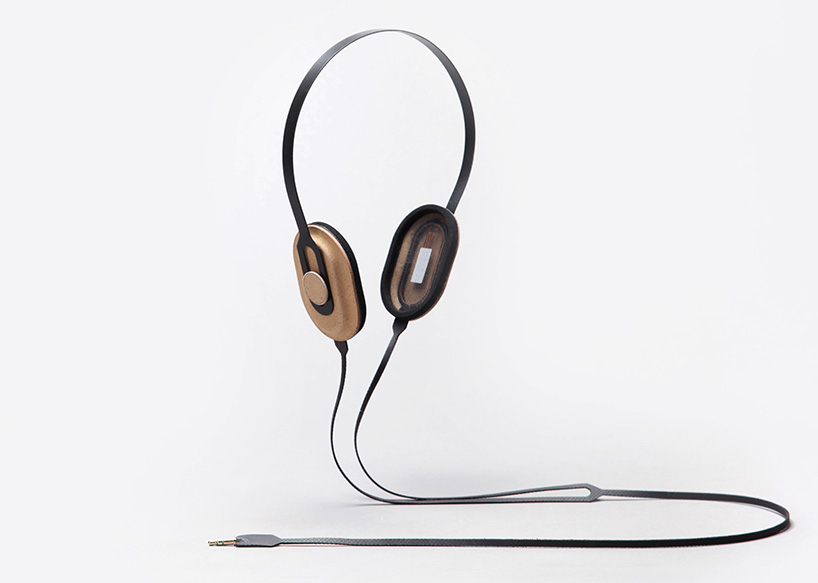
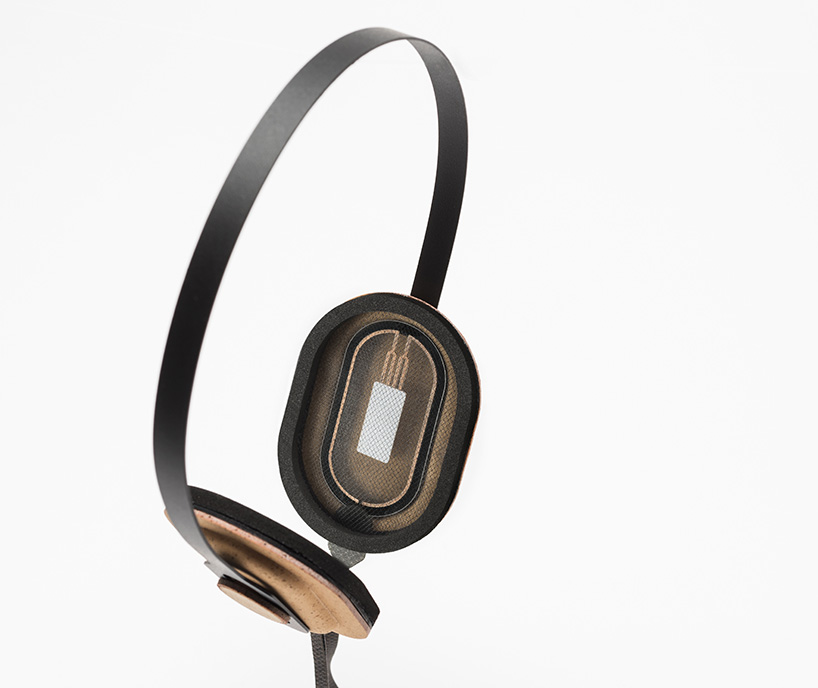
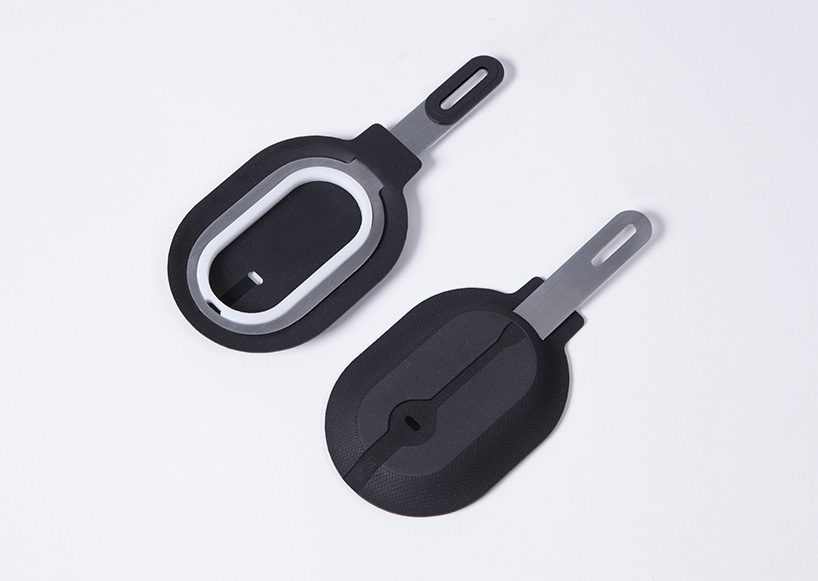
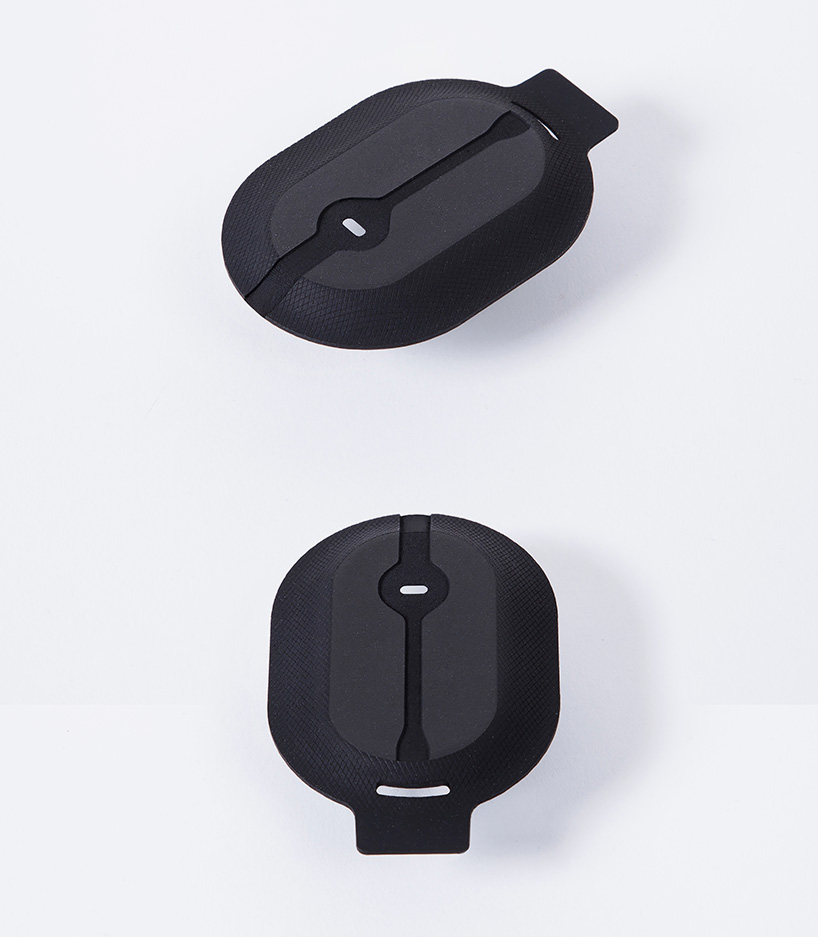
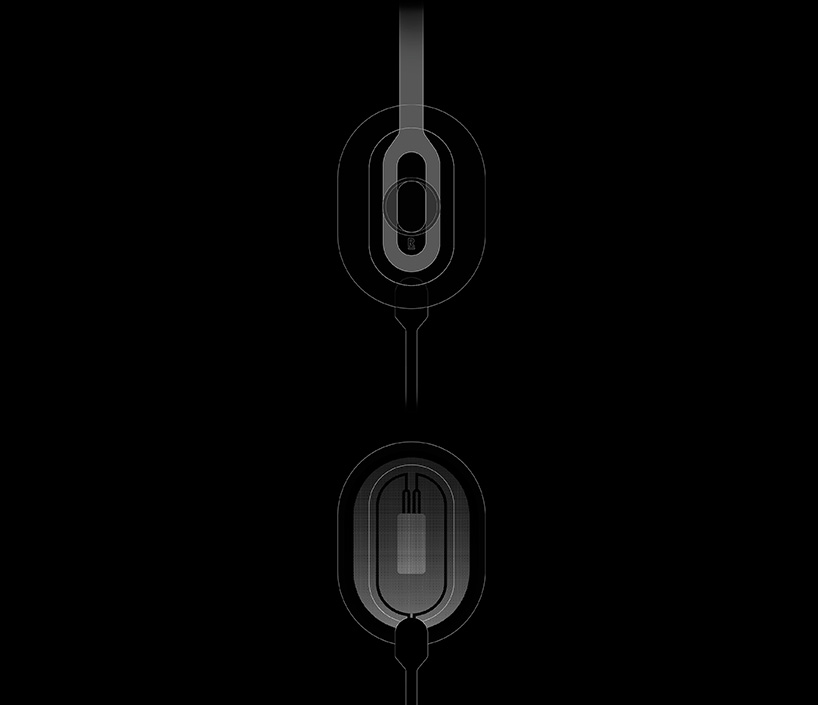
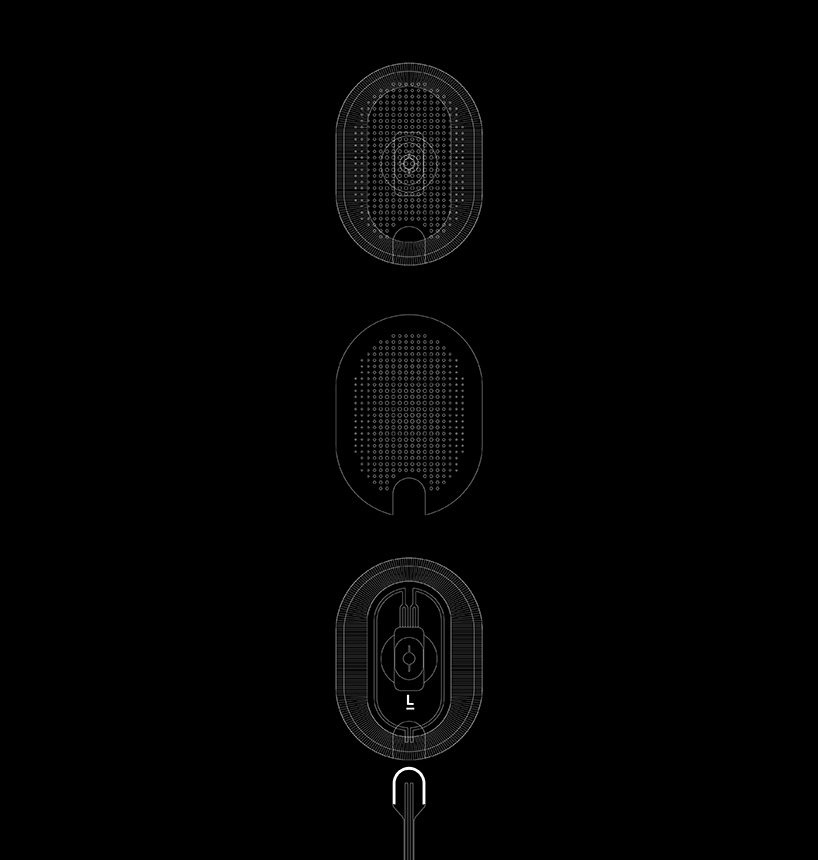
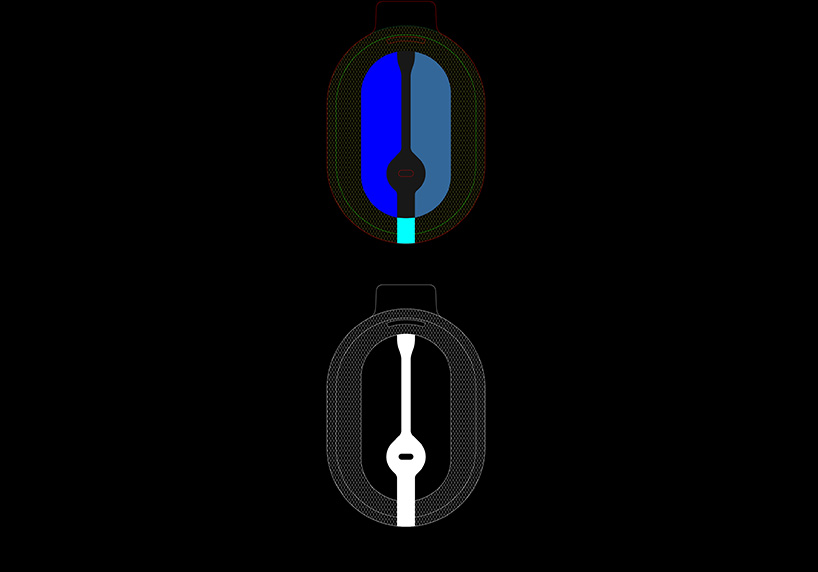
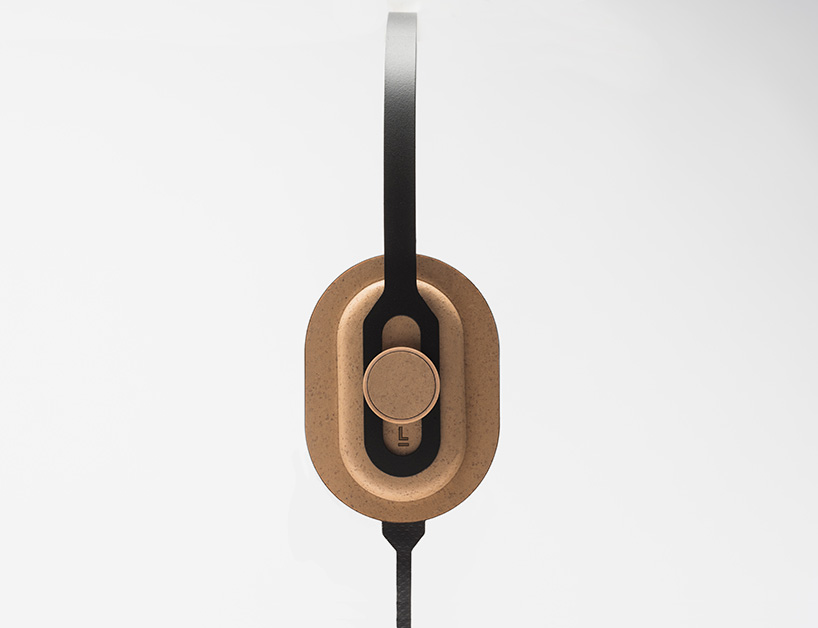
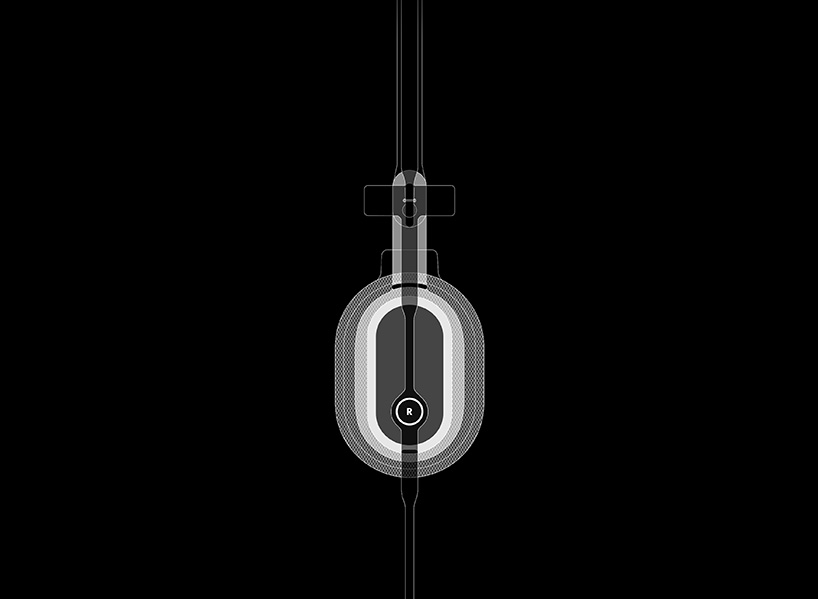
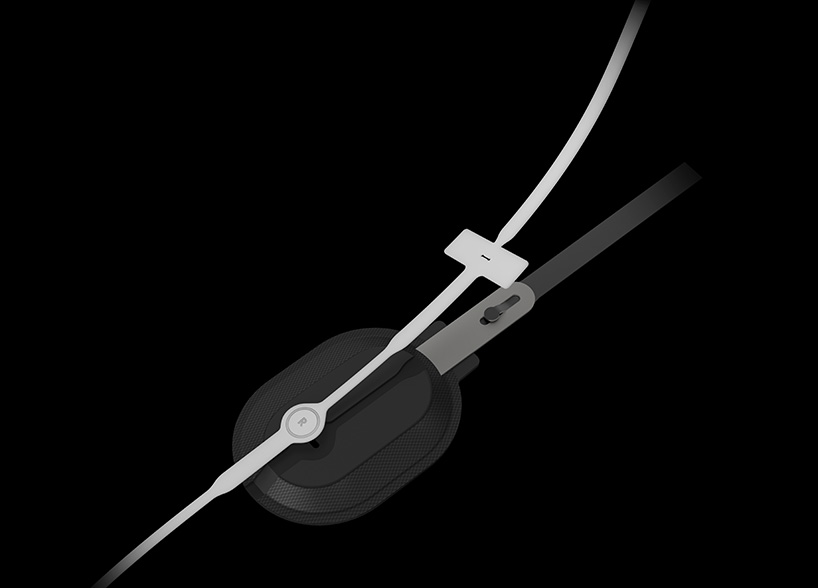
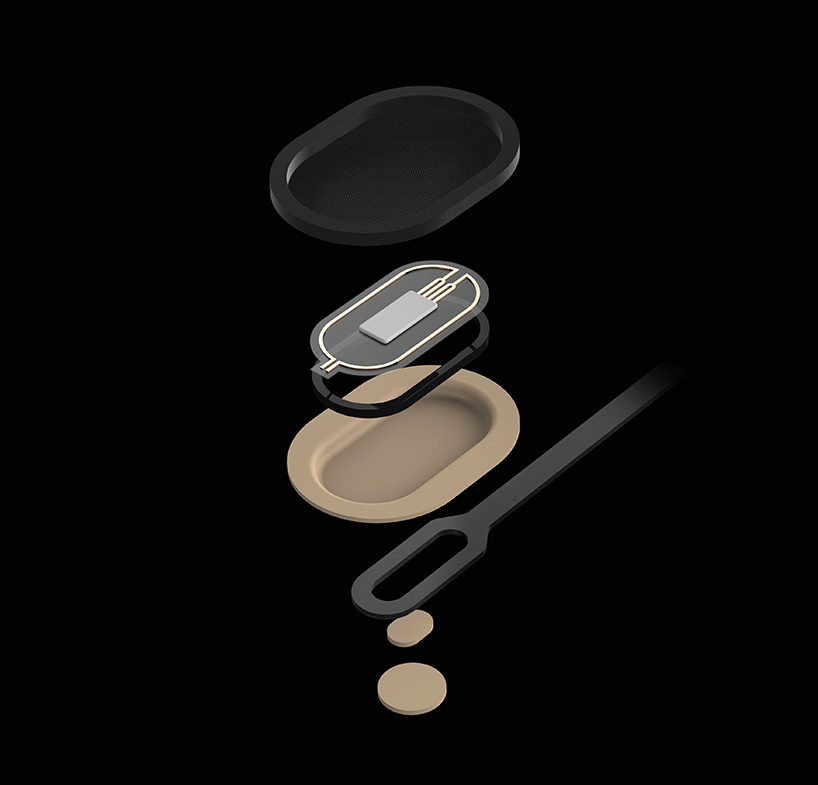