‘maestrie is the tale of a dimension up until now hidden away’…
words by carlo urbinati, chairman of italian lighting force foscarini, echo the sentiment and sensibility of the brand’s monumental cultural project, maestrie. an extensive undertaking that brings together the minds of artists, architects, authors, directors, and more, maestrie sheds light on the expert craftsmen and masterful makers who lie at the heart of foscarini’s production. ‘I wanted to find a way to convey the emotions I feel every time I visit the craftsmen who actually make our lamps,’ urbinati continues. ‘I am always fascinated by the extraordinary things that can be done.’
designboom was invited on an exclusive trip to venice to visit the foscarini headquarters and the factories where some of company’s most iconic products are made, unearthing the essence of maestrie in unparalleled intimacy.
inside the faps factory, where lamps like ‘twiggy’, ‘tress’ and ‘mite’ are made
as a focus, the mission of maestrie is to shed light on the humans behind the hardware, the passion behind the process, and the soul behind the highly skilled workforce that goes into a foscarini lamp. otherwise unknown to the everyday consumer is the incredible cast of master craftsman behind-the-scenes, each who have honed their skills over decades to be able to manufacturer some of the extraordinarily complex objects foscarini produces. glassblowers, fiberglass experts, concrete pourers, and painters all participate in a creative choreography with each other and with machines, working passionately to produce some of the most exceptional objects of italian design.
‘mite’ floor lamps are carefully made by hand
to help tell this new chapter in foscarini’s story, the company enlisted several creative protagonists. artist gianluca vassallo became the vessel through which the narrative unravels, going inside three factories in northern italy that collaborate closely with foscarini on a range of models. vassallo intimately documented the man-made making-processes in an unconventional way, taking portraits of the faces and hands of craftsmen, pictures of the masters at work, and images of the raw materials. video documentation invites a wholly artistic perspective into the ingenuity and know-how of each master craftsman.
patterns for the forms are cut by hand
‘I am periodically reminded of the valuable observation made by enzo mari in a conversation from a few years ago,’ writes maestrie contributor and architect manolo de giorgi an essay about the project. ‘at that time, during a chronological review of the tangible contribution made by various entrepreneurs to the fortune of italian design, mari pointed out with his radical outlook how it wasn’t true that italian products were simply industrial, but rather had always been ‘designed as industrial but were actually hand-crafted’. this subtle and skeptical view came about after a veil of illusion had been cast over it, in other words a heavy hand had been placed for too long over an industrial reality that was apparently entirely visible, an illusion that concealed the reality of things, a reality that was instead well hidden somewhere else entirely.’
shades for ‘twiggy’ are individually sprayed
to uncover this ‘reality’, designboom visited a few of the factories that have collaborated closely with foscarini for decades.
faps is based about an hour outside of the city of venice, and is responsible for the production of foscarini’s ‘mite’, ‘tress’ and ‘twiggy’ lamps. specializing in composite materials like fiberglass and carbon fibre, faps was largely involved in the production of fishing rods — an interesting nod to ‘twiggy’s’ thin and lightweight form. upon realizing the potential application of fiberglass and carbon fibre in furnishings, foscarini — together with designer marc sadler (the mind behind ‘mite’, ‘tress’ and ‘twiggy’) — began a passionate and prosperous collaboration.
workers check the quality and opacity of the shade using light
the lamps manufactured at faps are fabricated following complex recipes developed by in-house experts and master makers. here, countless human hands — whether carefully cutting fiberglass fabric sheets for ‘mite’, intricately spinning material ‘ribbons’ to form ‘tress’, or individually checking the precise opacity of ‘twiggy’ shades — contribute to the form and superb quality of the final product.
‘tress’ is spun from coated fiberglass-based composite material
nearby, vetrofond is working on another kind of production entirely — glass. the company left murano in the 1990s to settle on the mainland of venice, at the same time foscarini was looking to combine the tradition of blown glass with technology in tune with the times. the now iconic ‘lumiere lamp’ designed by rodolfo dordoni at the time became a monumental catalyst for the collaboration between foscarini and vetrofond. over the years, the companies have established a working relationship that puts a deep emphasis on craft, and recognizing the manufacturing quality vetrofond is capable of providing.
lamps manufactured at faps are fabricated following complex recipes
inside the fiery facility, masters are working on individually blowing forms for newer lamps like ‘tartan’ and ‘rituals’, by ludovica+roberto palomba. wielding rods capped with intensely-hot molten glass, the blowers elegantly and effortlessly make their way around the factory and shape the liquid material using metal molds. incredible attention is given to each and every object by masters and apprentices alike — an intense passion for the work is almost palpable.
inside vetrofond, a facility which works on the production of foscarini’s glass lamps
finally, crea is working with yet another of foscarini’s material favorites. the small company is where the ‘aplomb’ lamps by paolo lucidi and luca pevere are produced in concrete. initially, the idea was dampened by the retort ‘it cannot be done’ by crea’s founder giovanni piccinelli, upon seeing the thinness proposed by the design duo. but despite initial restraint, the curious craftsman developed a unique way to make the technical specifications work, using their expertise to eventually come up with a formula that had never before been used.
masters are working on individually blowing forms
‘giovanni piccinelli has always been a curious craftsman. an inventor. someone who discovers things,’ writes professor stefano micelli in his essay on maestrie. ‘like many of the great italian artisans, he has never lost his taste for trial and error, experimentation. he has always had a passion for playing with new mixtures, new materials. making molds is an ability piccinelli has developed through his own initiative, his own stubborn effort. first with the help of a specialist, then as an autodidact, often spending weekends on attempts to invent something new. paolo lucidi and luca pevere understood him: working with entrepreneurs like piccinelli is a pleasure, and the only problem is to find a pretext to have fun finding original solutions. the most outlandish technical challenges are the best excuse to discuss things and to test one’s reasoning.’
makers wield rods capped with intensely-hot molten glass
‘maestrie’ is a continuation of foscarini’s monumental mission to unearth each lamp as a passion project, particularly by spotlighting the humanity behind the know-how.
‘the objective is to acknowledge the value that has been created by the firm’s most prestigious designers and to bear witness to the role and importance of the skills that go into the high quality and aesthetic value of the company’s products,’ micelli continues. ‘foscarini’s tribute sets out to celebrate social and cultural values. the interplay of relationships and efforts that gives rise to such ambitious projects deserves to be illustrated and thus widely understood and appreciated.’
the blowers elegantly and effortlessly make their way around the factory floor
the liquid material is shaped using metal molds
incredible attention is given to each and every object by masters and apprentices alike
crea is working with yet another of foscarini’s material favorites — concrete
the small company is where the ‘aplomb’ lamps by paolo lucidi and luca pevere are produced
despite initial restraint, the craftsman developed a way to make the unique technical specifications work
crea originally comes from the world of construction
crea has radically changed its way of operating on the market
‘aplomb’ is a small hanging lamp offered in six, colored finishes
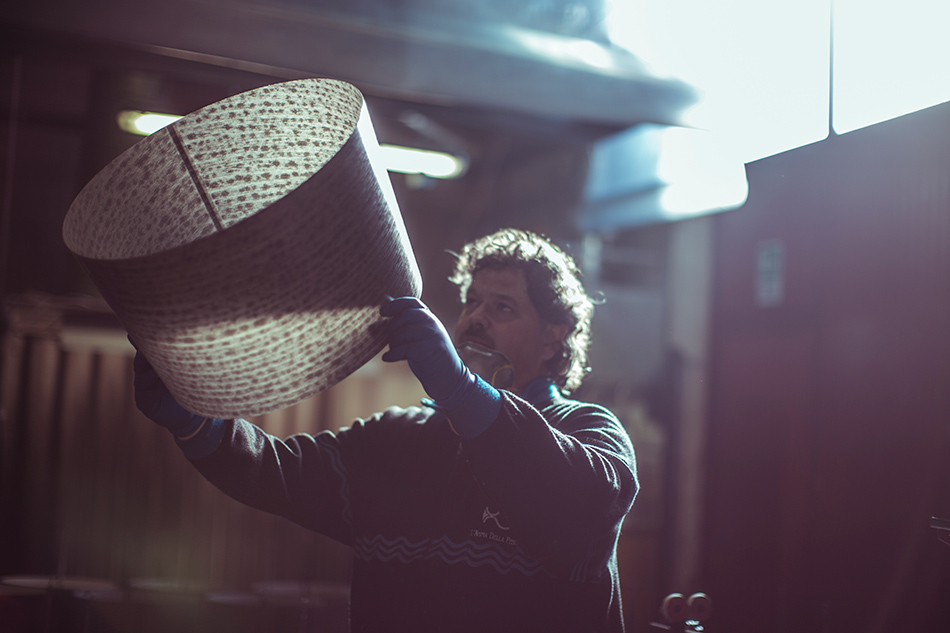
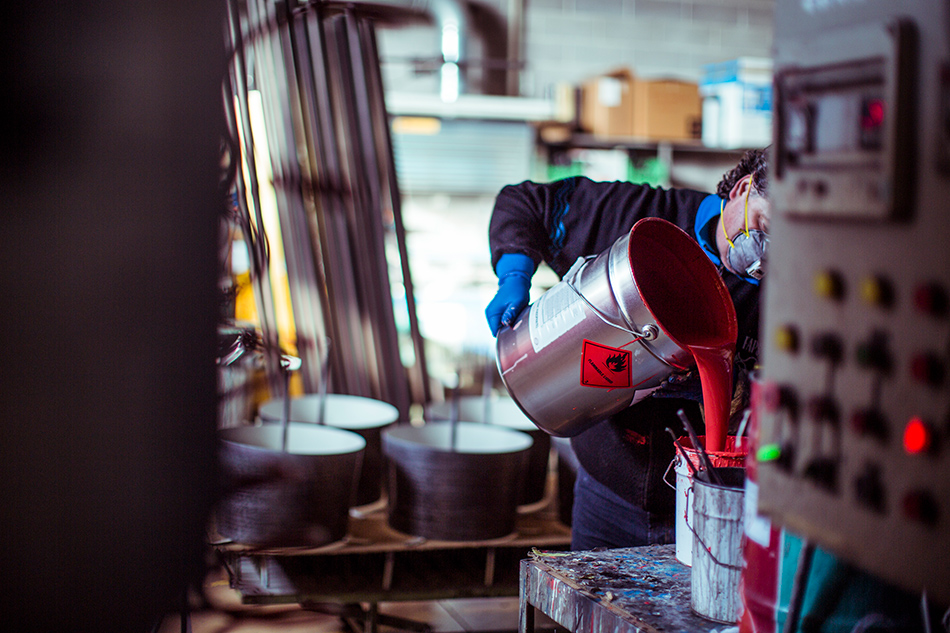
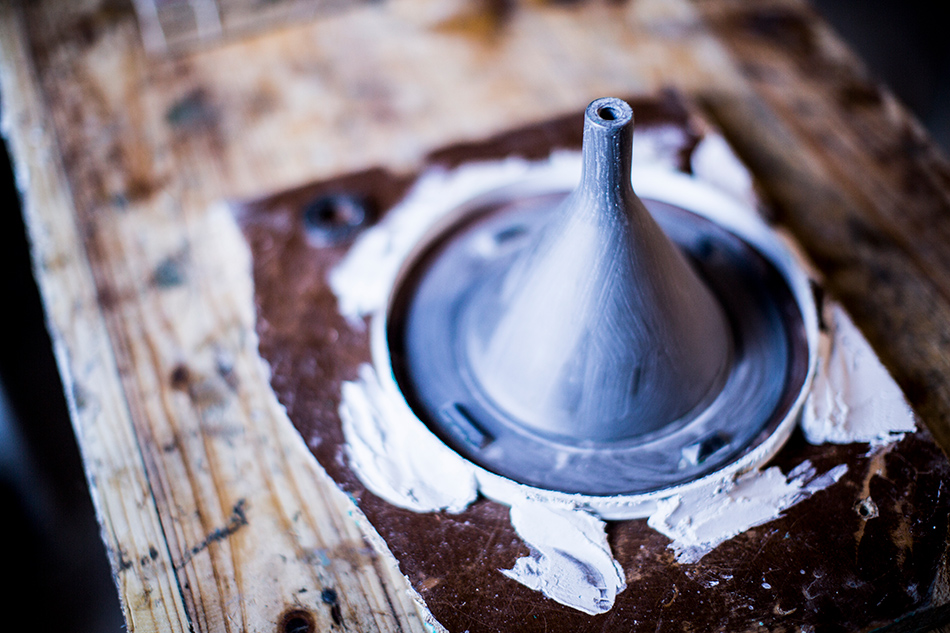
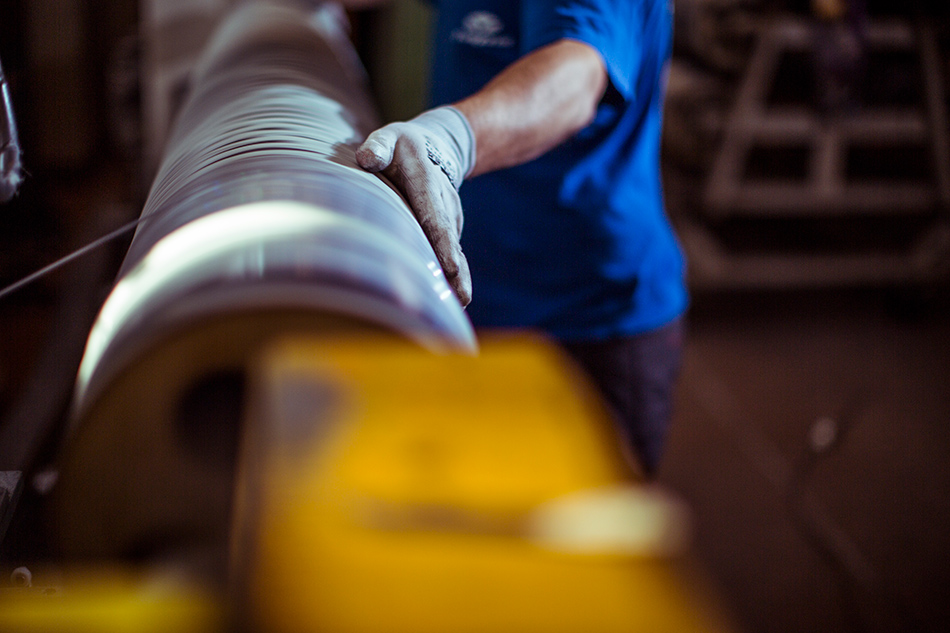
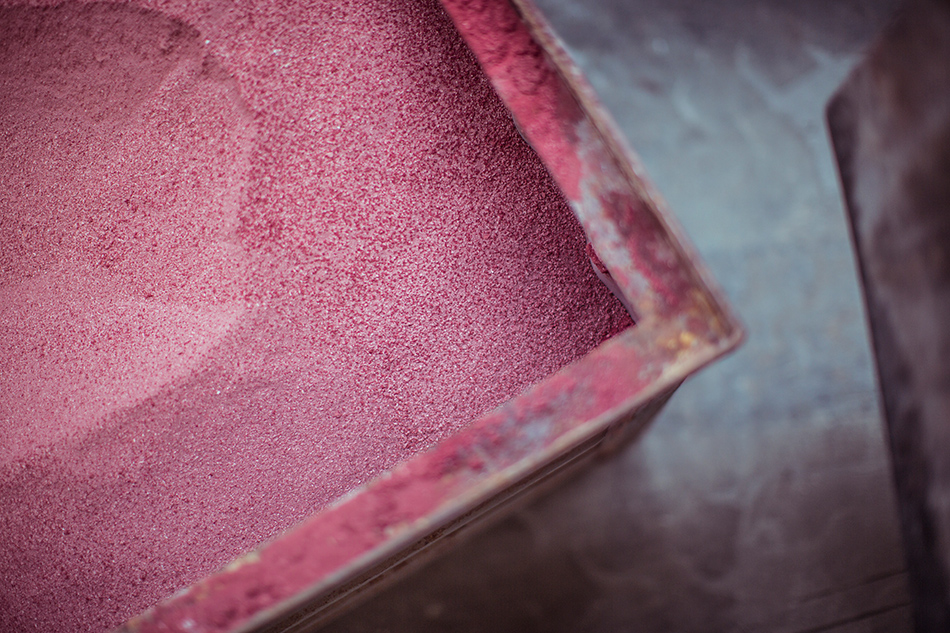
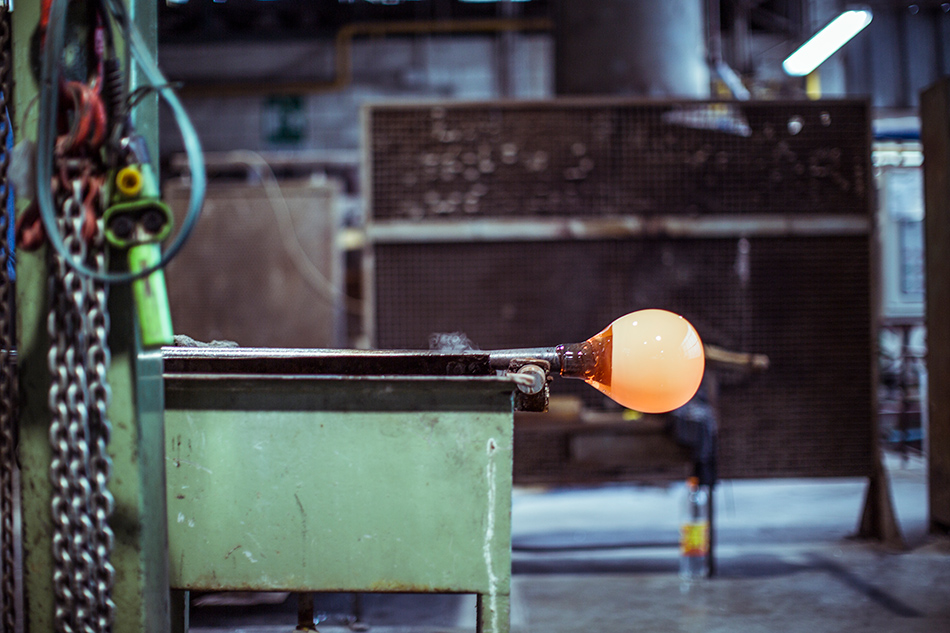
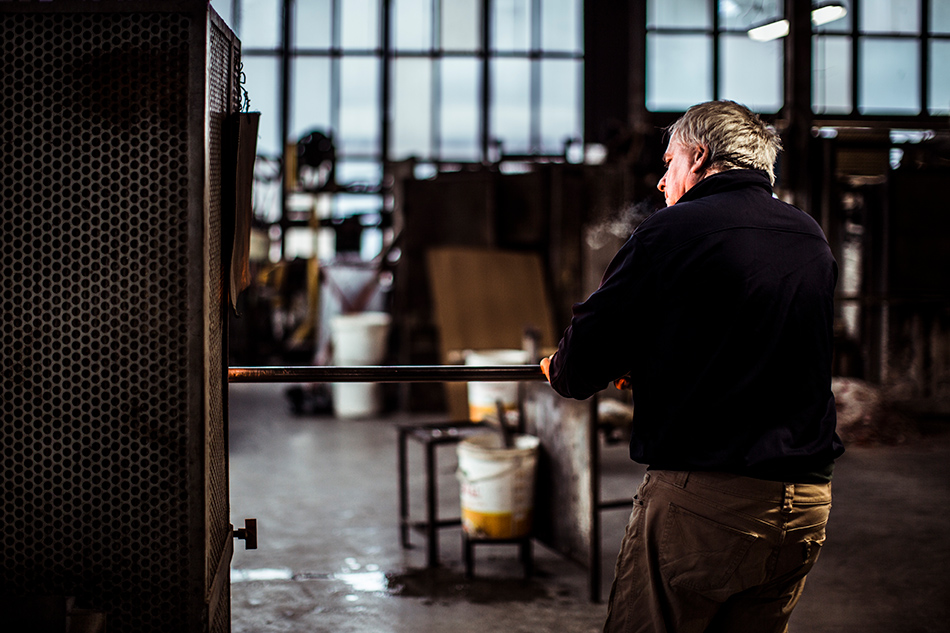
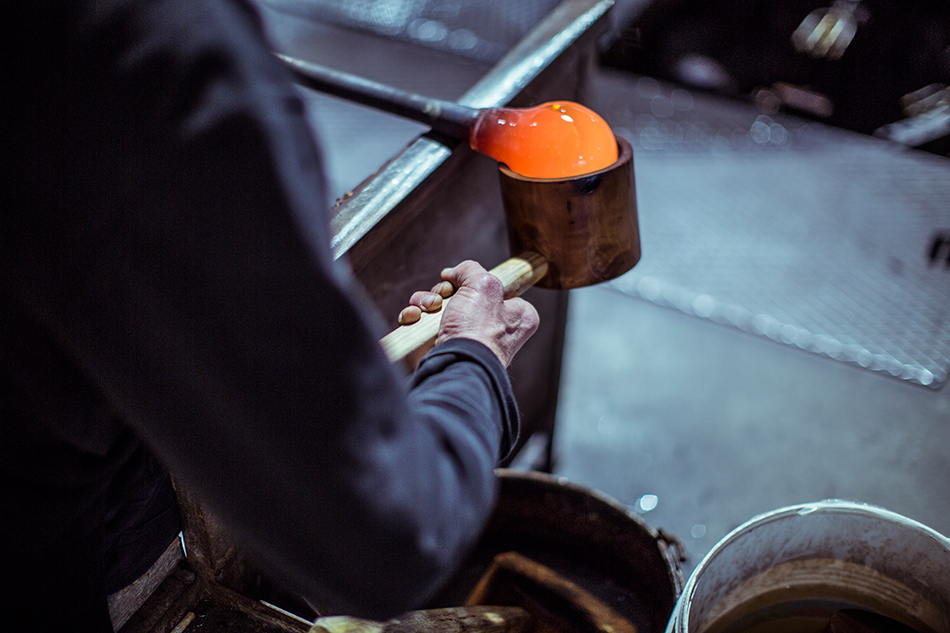
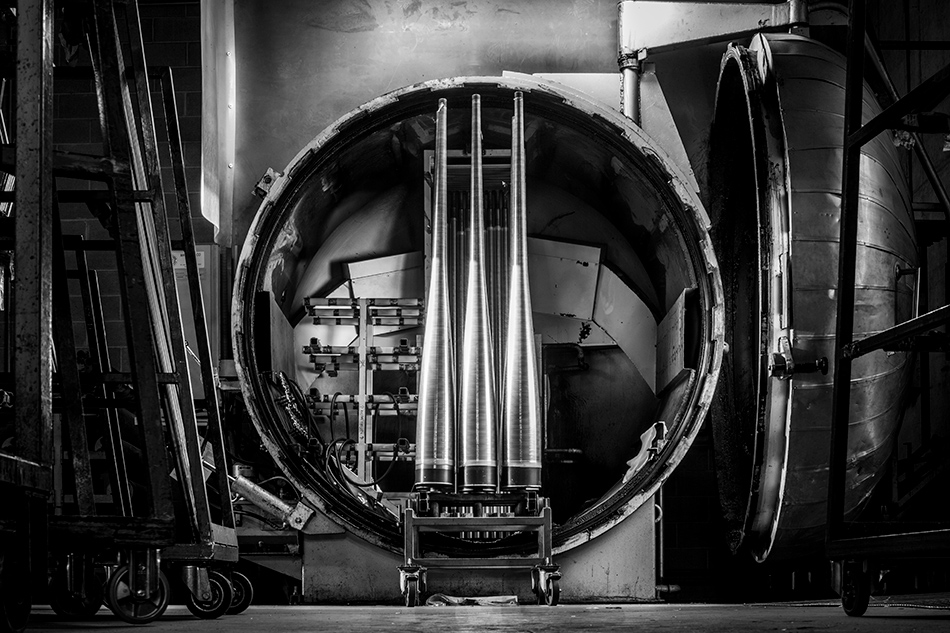
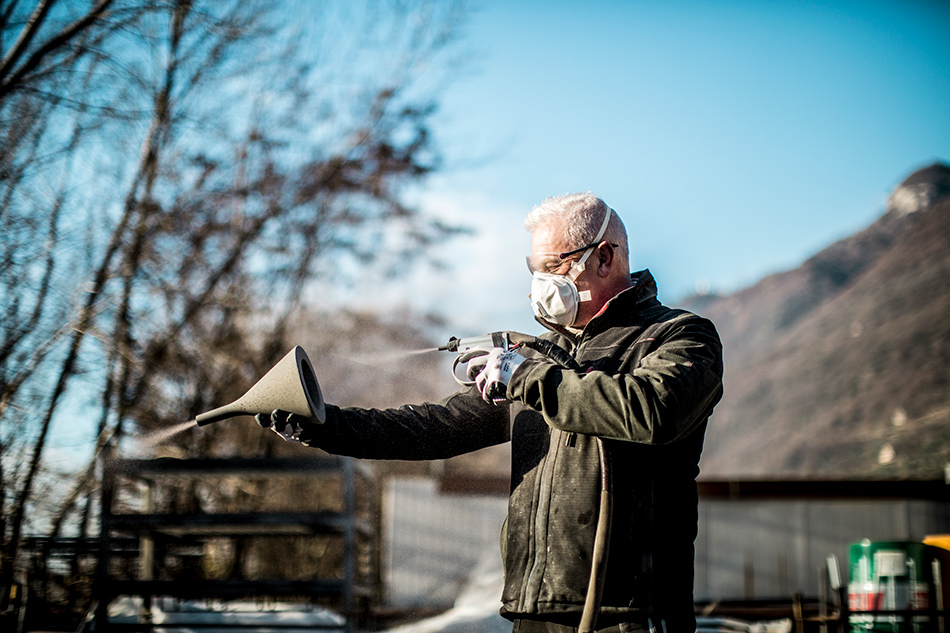
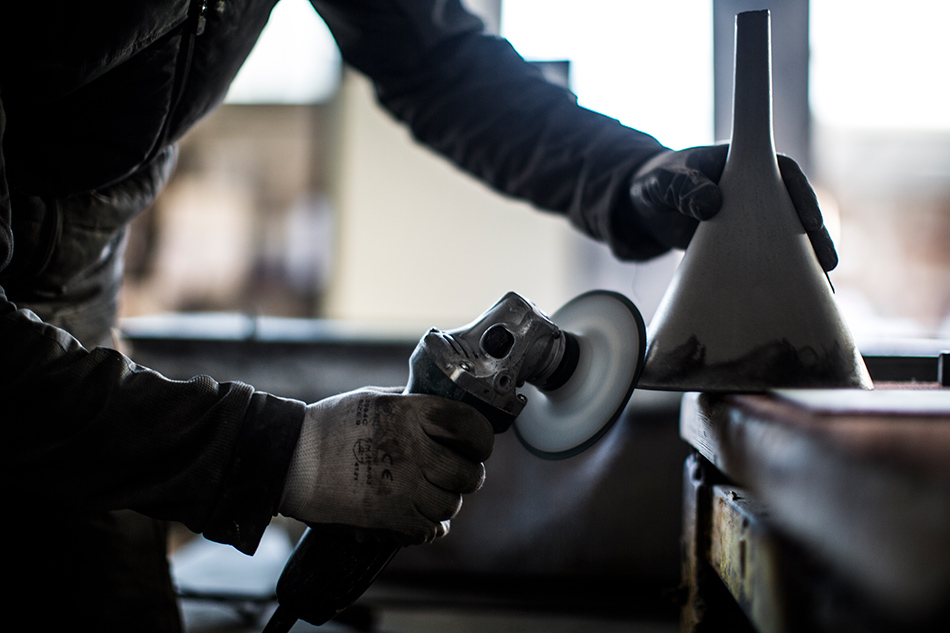
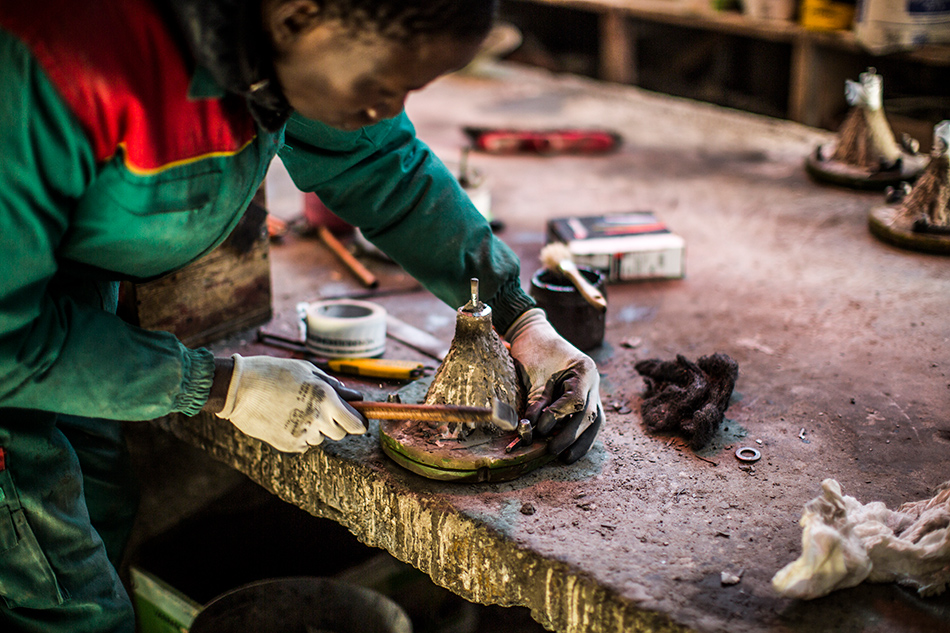
PRODUCT LIBRARY
a diverse digital database that acts as a valuable guide in gaining insight and information about a product directly from the manufacturer, and serves as a rich reference point in developing a project or scheme.