this three-meter-tall pavilion is composed of two adaptive folding elements, which have been programmed to open and close like the wings of a ladybird. collaboratively conceived and fabricated by three institutes at the university of stuttgart in germany, the project — referred to as the ITECH research demonstrator 2018/19 — is made from carbon and glass fiber-reinforced plastic and is the first of its kind to employ industrial tape-laying technology for an automated fabrication of large-scale compliant mechanisms. the project is part of a series of research demonstrators showcasing the potential of computational design, simulation and fabrication processes in bio-inspired architecture.
all images and video © ICD/ITKE/ITFT university of stuttgart
the structure has been realized by the institute for computational design and construction (ICD), the institute of building structures and structural design (ITKE), and the institute for textile and fiber technologies (ITFT) — three faculties at the university of stuttgart. the project was designed and realized by students and researchers, supported by a multi-disciplinary team of architects, engineers, biologists, and paleontologists. inspired by the folding wing mechanisms of the coleoptera coccinellidae — otherwise known as the ladybird (UK), or ladybug (US) — the team sought to investigate large-scale compliant architecture.
an initial biomimetic investigation preceded design development to identify functional kinematic principles which could be abstracted and transferred to technical architectural applications. the group soon identified the origami-like folding patterns of ladybird wings as a biological role-model. ‘many beetle species cover their thin and fragile hind wings with more robust forewings,’ explains the team. ‘in order to compactly pack them under the forewings, the wings fold along distinct flexible hinge zones with specifically defined mechanical properties. folded, elastic energy is stored in the hinges to enable a rapid unfolding in case the insect must escape danger.’
‘those patterns can be mathematically described as flexagons, a common origami folding pattern,’ the team continues. ‘through analysis and mathematical geometric descriptions, it was possible to investigate and abstract the kinematic behavior, enabling distinct elastic hinge zones to be materialized with specifically programmed material gradients within the fiber-reinforced plastic.’
utilizing the elastic deformation of distinct flexible hinge zones to enable spatial reconfiguration, the demonstrator explores the potential of utilizing fiber-reinforced plastic materials in large-scale kinetic folding systems. thanks to an interactive control system — consisting of integrated sensors, online communication, and backend computational processing — the wings can be moved either by a physical touch or remotely via a connected device. read more about the project here.
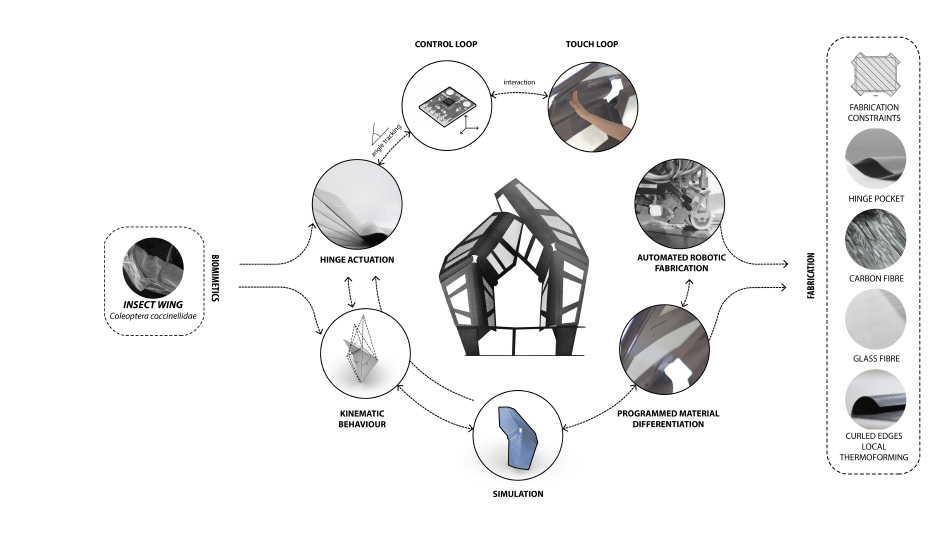
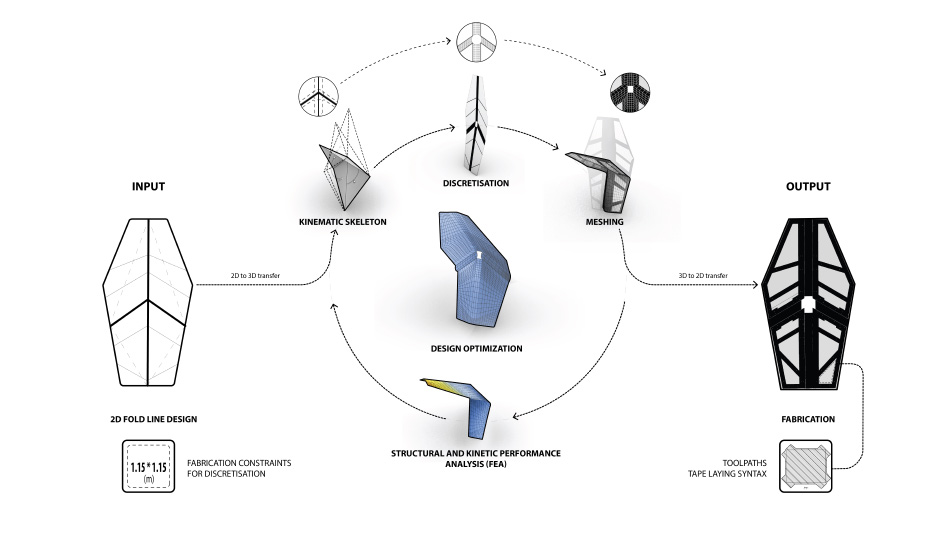
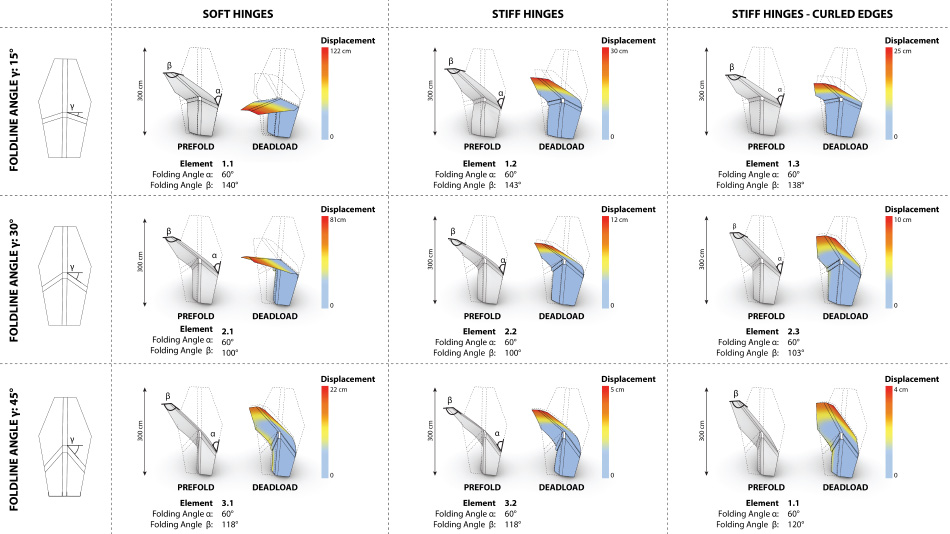
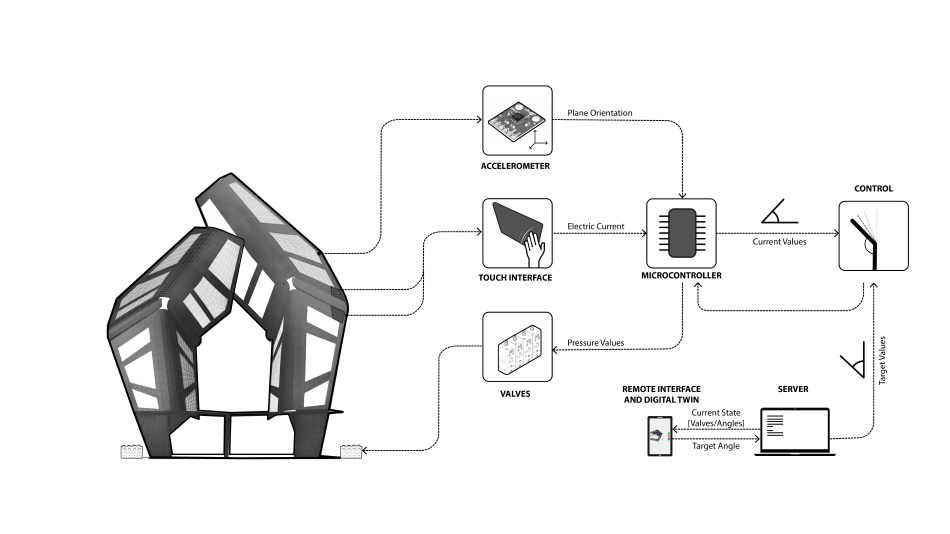
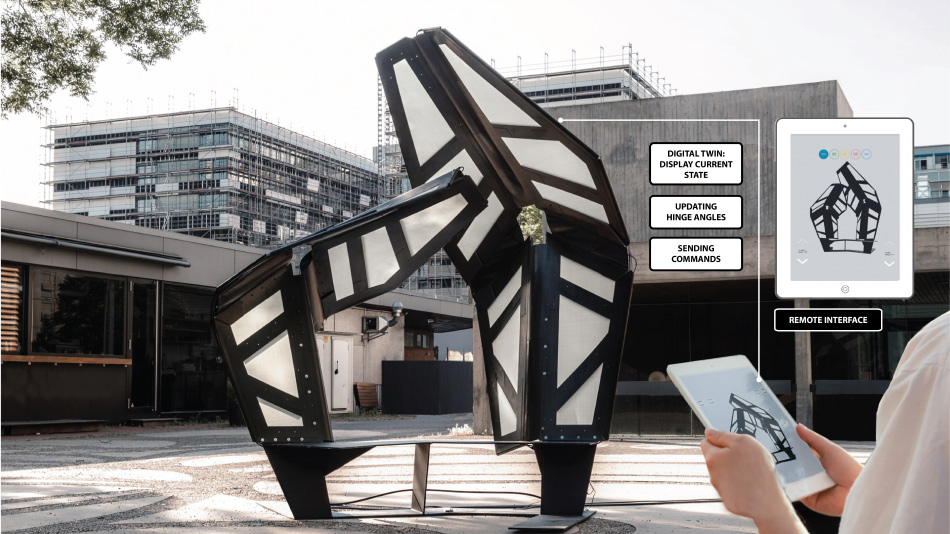
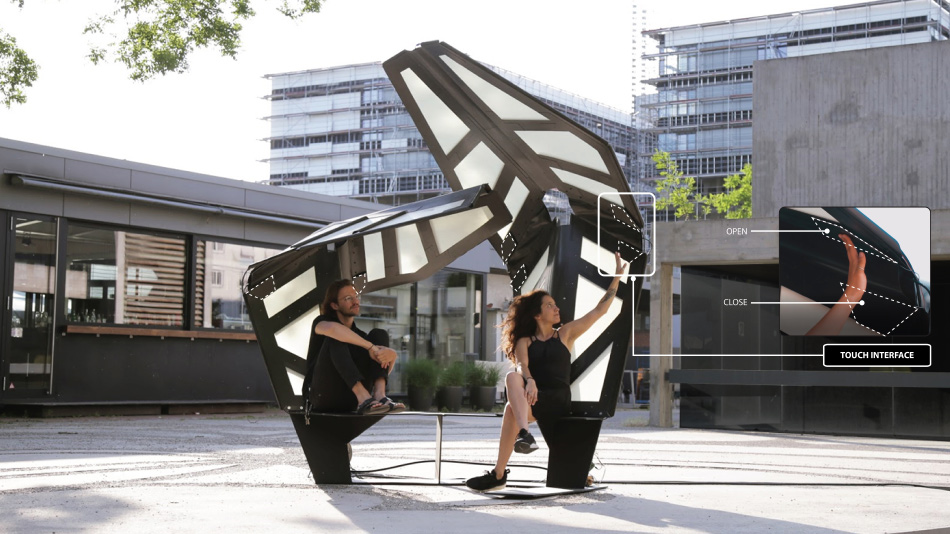
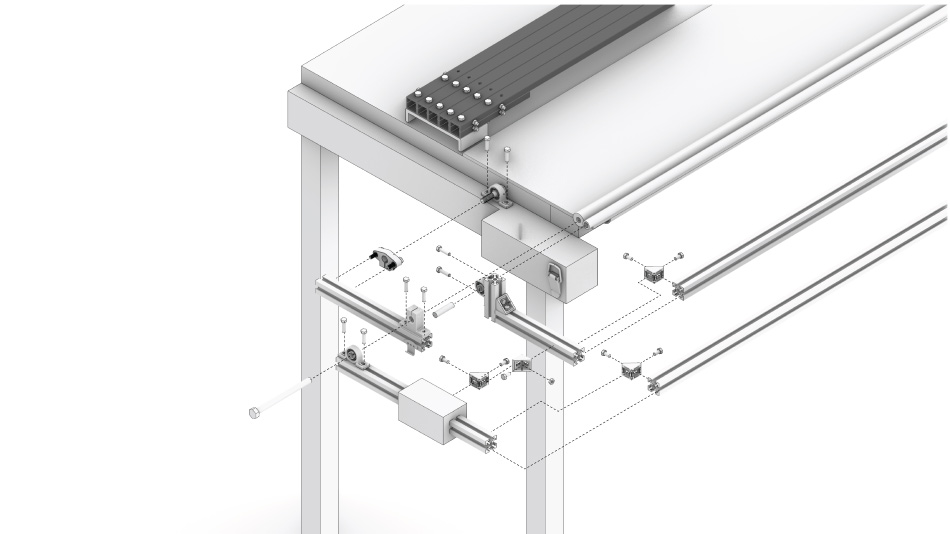
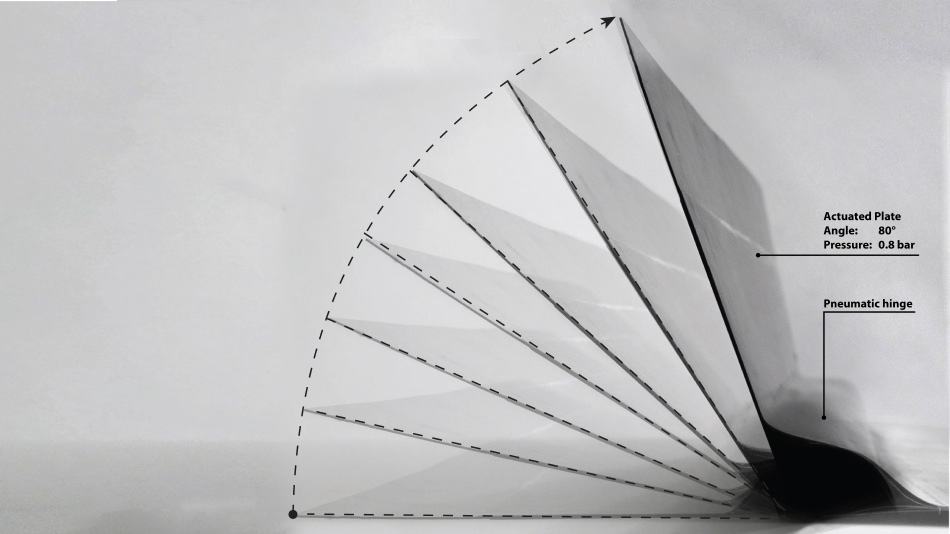
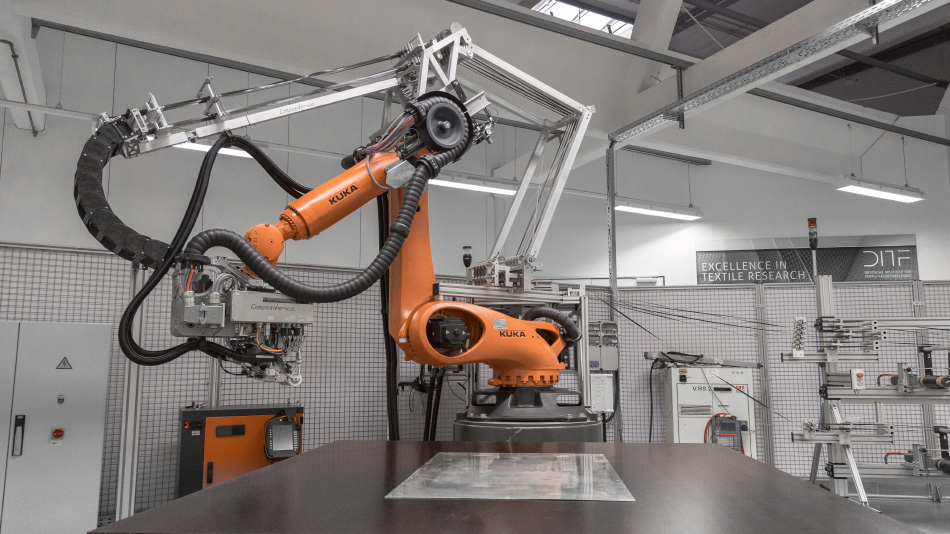
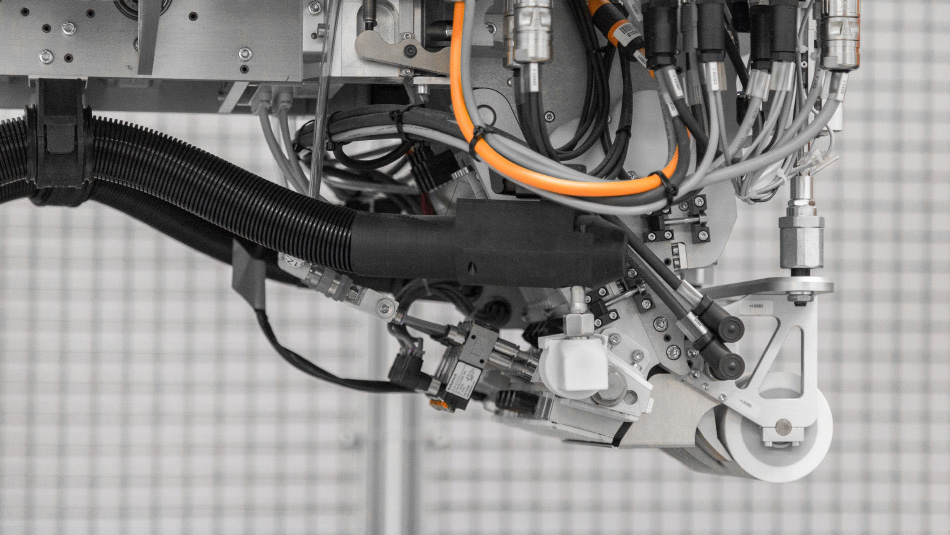
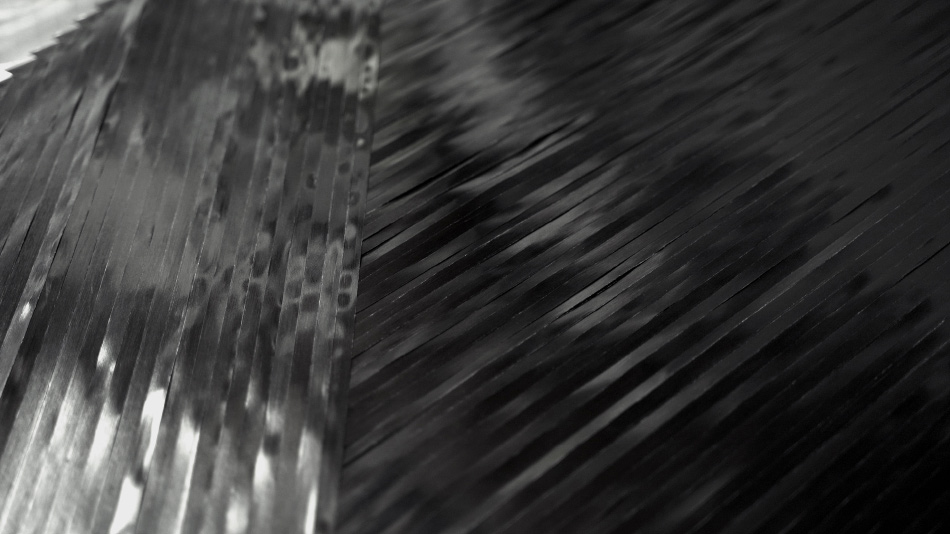
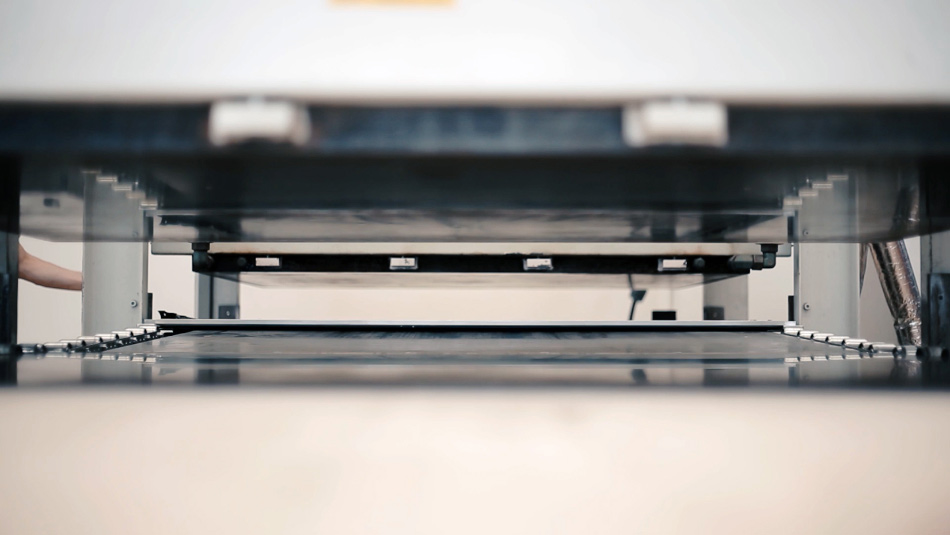
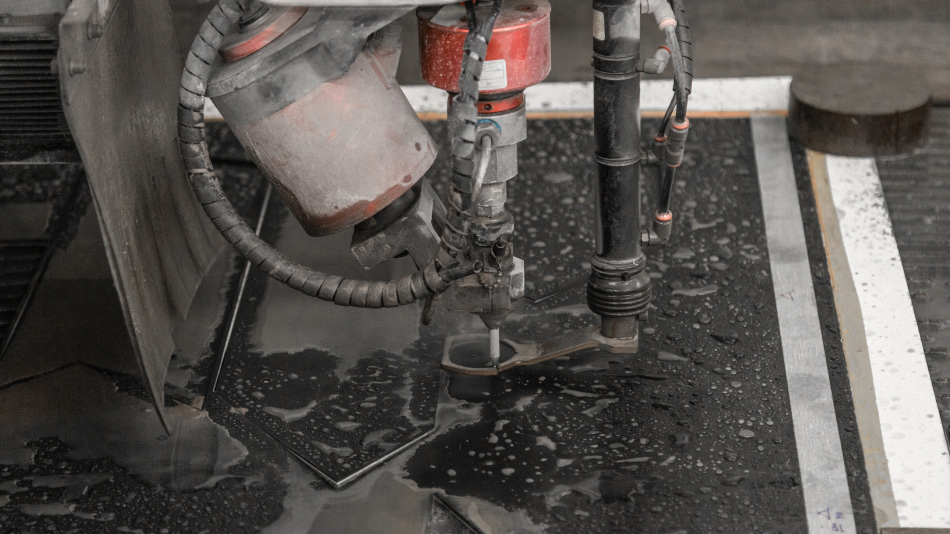
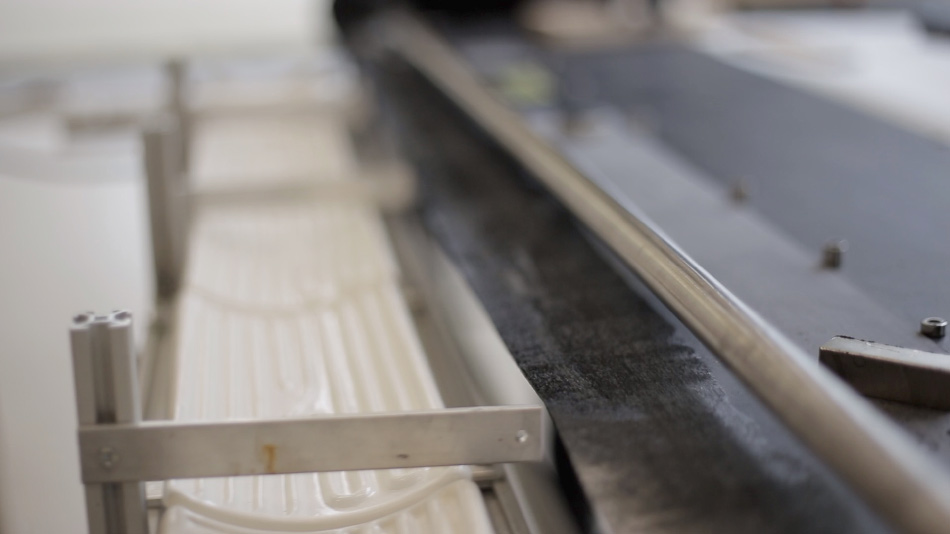
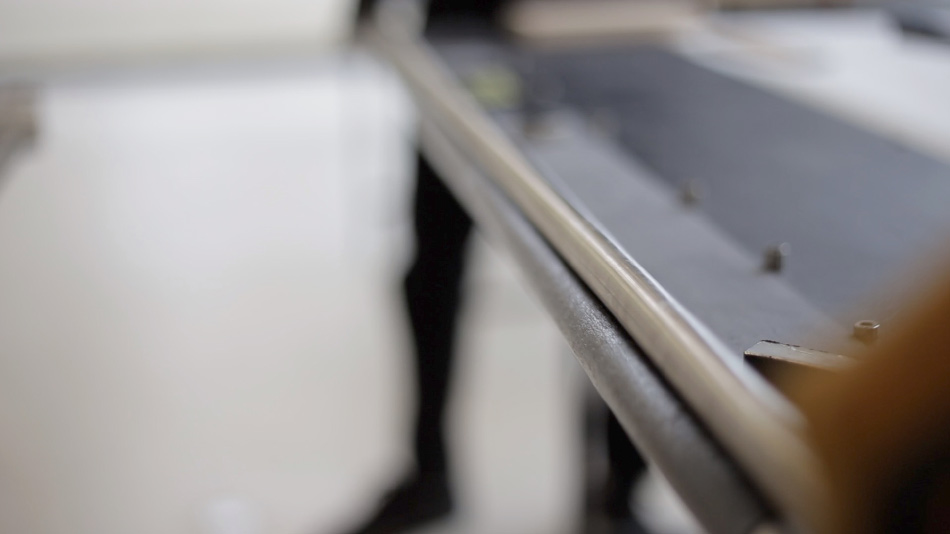
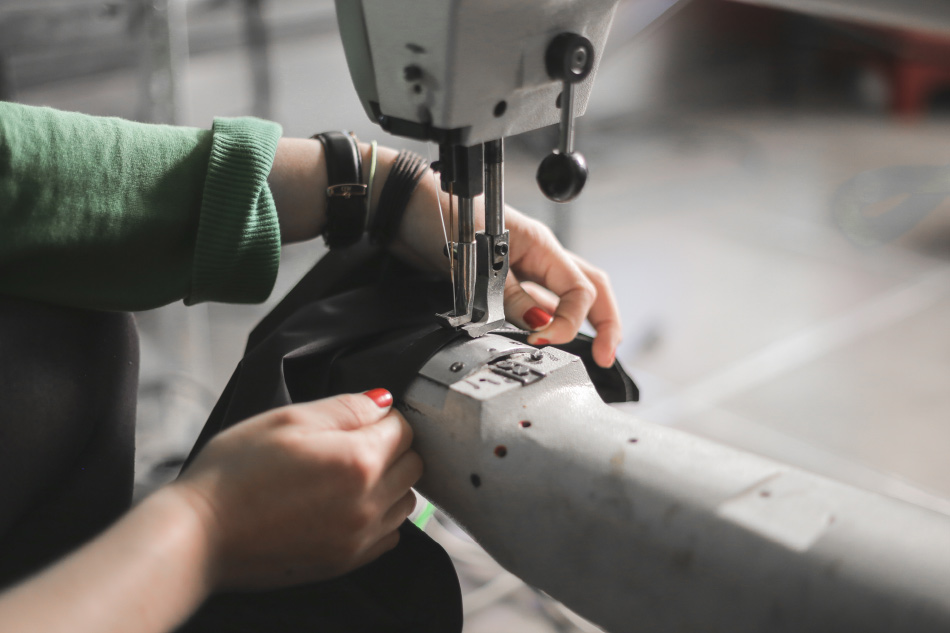
project info:
location: keplerstr. 11-17, 70174 stuttgart, germany
completion: june 2019
component size: 3.00 m x 1.70 m and 2.50 m x 1.70 m
component weight: 23 kg per element
project team:
ICD institute for computational design and construction – prof. achim menges
ITKE institute of building structures and structural design – prof. dr.-ing. jan knippers
ITFT institute for textile and fiber technologies – prof. dr.-ing. götz t. gresser
scientific development: axel körner, larissa born, oliver bucklin, seiichi suzuki, lauren vasey
concept development, system development, fabrication & construction: miro bannwart, eliza biała, xiaoyu chen, rebeca duque estrada de almeida araujo, farnaz fattahi, rob faulkner, david horvath, niloofar imani, you-wen ji, fabian kannenberg, nate kaylor, denitsa koleva, jure kozmos, i-ching lee, ada leżuchowska, zhiqi lin, samantha melnyk, seyed mobin moussavi, mona mühlich, seyed ahmad razavi, tamara rosales, emi shiraishi, sanoop siby, piyanat songkhroh, hana svatoš-ražnjević, naomi kris tashiro, babasola thomas, aditya tiwari, maria wyller, nima zahiri, ruqing zhong
with support of: anja mader, katja rinderspacher, maria yablonina
in collaboration with: compositence GmbH
department of evolutionary biology of invertebrates – prof. oliver betz
department of palaeontology of invertebrates – prof. james nebelsick
university of tuebingen
supported by: autodesk;
roy hohlfeld