arduino factory + production tour
image © designboom
who would ever imagine that global cultural and economic revolution would spring from the tranquil fields of piedmont, italy, in tiny towns nestled against the stunning backdrop of the alps? but that’s exactly where arduino, the system of microcontrollers revolutionzing the maker movement and pioneering the concept of opensource hardware, was born in 2005 and continues to make its home today.
arduino’s story is unusual to say the least. five colleagues, seeking to empower students with the tools to create, developed the platform in 2005. now distributors estimate that over one million arduinos have been sold, and the arduino community is among the most resilent and inventive on the internet. forums like instructables and arduino’s own scuola connect enthusiasts to learn from one another, and arduino users build on the platform to open up new creative possibilities.
we traveled to turin, italy, to see arduino’s first officina, before setting off north to visit the italian factories that continue to be the heart of arduino manufacturing for the entire world.
the citofono to the torino officina arduino, nameplate CNC-engraved at their fablab
image ©designboom
located in what’s known as the ‘capital of the alps’, the torino officina was founded in february 2012 to oversee the development of the hardware and expand the educational and cultural initiatives that surround it. davide gomba, already an arduino veteran by the time, was among the associates instrumental in founding the office, and we’re lucky to have him as our guide throughout our visit. it’s late august when we arrive, and some of the office is still on summer holidays, but those who are there are hard at work preparing for the release of two new arduino products and organizing the rome maker faire in collaboration with make, asset-camera, and tecnopolo.
this officina is also home to italy’s first hackspace, the torino fablab, where makers share production equipment and tips as well as ideas and conversation in a workshop outfitted with four 3D printers, a sewing machine, two CNC routers, soldering irons, woodworking tools, and other equipment.
it’s ushering in the next stage of a long history of production and innovation for piedmont’s capital city. FIAT was established here in 1899, and turin’s history as an industrial powerhouse lives on today, most notably through the operations of car manufacturers as well as its thriving aerospace industry, where modules of the international space station were produced.
showing its italian pride in red, white, and green, system elettronica develops arduino’s PCBs for the global market right here in strambino, italy, using mostly locally produced machines
image © designboom
it isn’t long before we’re in the car enroute north to see where arduinos are made. the arduino production facilities are actually spread across three factories in piedmont, all along the outskirts of the town of ivrea. at system elettronica in strambino, the circuit boards themselves are manufactured, arriving to the factory as mass-produced sheets of copper and leaving identifiably as arduinos, coloured blue and white and circuit designs etched for the later embedding and assembly of their electrical componentry. a separate company, BCA, conducts some of the stages of assembly, while the electronic infrastructure is finished by hand and the products packaged and prepared for shipping at smartprojects in scarmagno.
system elettronica is our first stop. as owner ludovico apruzzese leads us around the factory, he explains that not only is the arduino hardware entirely made in italy but so are the machines that produce it. taking advantage of the industrial heritage of the region, much of his equipment is produced in the surrounding region of canavase, and many are driven by control circuits that apruzzese himself designs and produces in-house. he even makes the boards of the control circuits blue rather than the ordinary green, to match arduino’s characteristic colour.
these blue control boards are designed in-house custom for the arduino production line
image © designboom
system elettronica not only produces arduino’s PCBs but also the control circuits for the machines it uses to do so, which the factory owner makes blue to match arduino boards’ unusual hue. at system elettronica, the first step in the creation of an arduino board is a machine that punches out holes on sheets of copper vetrite, stamping out the spaces that will house the microchip and other electronic components, as well as those that will eventually permit makers to connect all kinds of sensors, screens, and input devices. here in strambino, apruzzese estimates, they punch about 2 million holes each day for their line of arduino production alone.
an arduino in the making: the future vias of the PCBs are punched into copper vetrite sheets
image © designboom
ludovico apruzzese, the owner of system elettronica examines a sheet of what will become arduino leonardos
image © designboom
holes punched, the sheets are brought to a larger room where rows of machines are at work. we are led to the largest of these, set against the windows: a series of acid baths across six holding tanks that will etch the circuit. as a factory worker secures the copper sheets at one side of the machine, a mechanical arm sweeps above the liquids to collect them, dip them into the first section of the bath, and then place them into the second where the rest of their journey is coordinated automatically beneath the surface. when completed, the arm lifts them from the water and returns them to the beginning, where the worker unfastens them and files them onto a loading rack.
WATCH: arduino PCBs are etched through acid baths in a 20-step system across six holding tanks
video © designboom
a worker unfastens the sheet of boards after they’ve been etched
image © designboom
the freshly etched sheets of arduinos remain the original copper colour of the vetrite upon removal from the acid baths
image © designboom
enraptured by the flow of these machines at work, it is easy to forget how rare it is that electronics be produced from start to finish entirely at home, whether that means italy or america. but arduino does not outsource any of its production abroad, and factory founder and owner ludovico apruzzese is proud that such advanced production is all “made in italy”. the walls are graced by a border of the stripes of the italian flag, which he draws our attention to with a smile, and the red of the windowframes is striking against white walls with green border. davide reveals another charming secret: all of the lines of production in this factory are named after apruzzese’s wife and daughters.
proudly made in italy: system elettronica decorates its factory walls with the stripes of the italian flag
image © designboom
the italian attention to design detail isn’t lost in the production process either: our next stop in the building is the machine that stamps the arduinos– their bodies already their characteristic blue after the acid bath– completely white, much of which will be dissolved away in the next step. the machine looks little different from an ordinary silk screener, and a worker individually places each sheet by hand by a worker onto the platform and then pulls down the press, recoating it with paint as needed. what arrived as blue and copper boards are now completely white on one side.
screen printing the arduino PCBs white
image © designboom
arduino leonardos lined up after being screen printed
image © designboom
inside one of the machinery rooms at the system elettronica factory
image © designboom
their next visit is to the “solder mask developer”, or ‘alessandra’ (one of the owner’s daughters, as you might have guessed). here most of the white is peeled off the boards, retaining the border along the soldering holes and for accents such as the arduino name. at this point, the base PCB boards are nearly complete. the final machine at system elettronica is the miller, where three precision heads finely cut along the sheets of boards to remove the outer border and so that the grid of boards can be easily separated from each other later on.
looking in on the three-headed milling machine
image © designboom
a stack of arduino UNOs, freshly milled but not yet separated apart or removed from their white border piece
image © designboom
WATCH: a compilation of the making of an arduino PCB at system elettronica
video © designboom
throughout their production, the boards have made occasional trips to an oven for drying; now they’ll undergo testing via automated machines in a dedicated control room. this will mark the first of many quality assurance tests to which arduino subjects its boards before they’ll ever be packed or shipped to anyone.
in fact, although arduino is an opensource hardware system– all the diagrams and information for their construction is freely available online and enthusiasts are encouraged to build their own from scratch– only two facilities in the world besides arduino itself are currently licensed to use the arduino name on the boards they produce, a precaution adopted to preserve the high standards of quality to which the company is devoted. sparkfun in boulder, colorado manufactures the arduino pro, pro mini, and lilypad; and gravitech in california produces the nano. for now, everything else is made right here in italy.
official arduino T-shirts spotted on the packaging floor of smartprojects in italy
image © designboom
from system elettronica, the circuitboards are brought to a nearby assembly plant called BCA. interestingly, not a single one of arduino’s factories in piedmont produces exclusively arduinos. each one maintains various production lines for other companies and products, making the entire network more of an ecosystem than the top-down approach employed by many major electronics manufacturers. ‘it makes it healthier,’ davide explains, because there is no single client on whose demands the factories depend.
in fact today we don’t visit BCA, where the sheets are cut and other aspects of the boards’ assembly takes place, because at the moment only automotive parts are on the factory’s production lines, one of BCA’s other major clients. instead we head straight to the final stop in the making of an arduino, smart projects in scarmagno. here the human element driving the production process is inescapable. flooded with natural light, the open floor of the first warehouse we visit is broken into work countertops and tables. here, operators compile together arduino’s starter kits, assemble boxes, and package the products, the very final steps of the entire process.
image © designboom
but there’s still much to see before arriving at that stage. we step outside to walk over to another building in this small complex of old industrial spaces, and arrive in the single room where all microcontrollers are outfitted with their electronic infrastructure, a process achieved through a combination of machine automation and hand-soldering. the “pick-and-place machine” is the mechanical half of the process and permits the precise placement of SMDs (surface-mount devices) like capacitors and resisters. reels of components are loaded into a feeding rack at the front of the machine, while the arduino PCBs– now in smaller sheets of only about twelve boards– are automatically loaded in from the left. the mechanical head whizzes around the boards, picking up individual components from the reels and placing them onto the PCBs. it’s relatively standard operating procedure for PCB production, but that doesn’t make the process any less mesmerizing to watch.
WATCH: one of several pick-and-place machines fits arduino’s electronic infrastructure onto the circuitboard
video © designboom
on a small screen mounted to the right of the unit, a grayscale image not unlike what one would expect to see under a microscope is being constantly adjusted and overlain with green and red rectangles. this, it turns out, is the view from the camera housed within the mechanical head, and it is searching for indicative markings on the PCB that it algorithmically matches to its map of component placement, as well as scanning its own activity to ensure the successful picking up and placement of parts from the reels.
closer view of the component reels on a pick-and-place machine at smartprojects
image © designboom
from here the arduinos pass into a soldering oven, where they are inundated with “waves” of solder at 200°C, achieving the through-all holes (vias) that make the devices ready for the final steps of hand-soldering as well as more versatile forbuilding electronics projects. along the far wall, tens of the machine’s source reels of SMD components hang organized in rows, ready for use.
one factory wall houses extra component reels, necessary to build in the electronic SMD infrastructure of the boards
image © designboom
just steps away from this machine at work, three employees sit at tables that have been pushed together, each one armed with an array of boxes in which sit alternately headers, power and ethernet jacks, and other components. they are the human and handmade side of arduino electronics, and working with rapid ease but obvious precision, they place pieces by hand or tweezer into the holes of the PCBs and solder them into place. at another nearby table, a woman is preparing the new arduino robots for production, the finished models stacked onto a shelf below her.
several smartproject employees at work hand-soldering larger components onto the boards
image © designboom
closer view of a solderer at work
image © designboom
before arriving at smartprojects, the PCBs are thoroughly tested before ever leaving the system elettronica production plant. but here, their electronic infrastructure finally in place, each arduino is examined again, most in this very room on a dedicated suite of computers where they are loaded with the firmware and tested for general functionality, the responsiveness of their indicator lights, and other key functions. if everything looks good, then they’re sent down to the packaging floor we saw earlier, off to become someone’s exciting project somewhere on the planet!
tested throughout their construction, arduinos are loaded with the firmware and subjected to a final examination by hand before ever being sent to the packaging floor. such rigorous testing puts the probability of a malfunctioning device at less than 1%.
image © designboom
WATCH: arduino gets a new home!
video © designboom
we were curious about where the story of arduino all began, so davide brings us to the former site of the interaction design institute ivrea (IDII), unfortunately closed in 2005. the striking building once housed offices of olivetti, the world-renowned italian typewriter manufacturer acclaimed for its attention to graphic and industrial design and makers of the first commercially produced personal computer in 1965. even now, the exterior remains essentially the same as it was when massimo banzi, david cuartielles, and gianluca martino worked here and developed what would become arduino: a founding team quickly joined by IDII graduate student david mellis, now arduino’s lead software developer, and early arduino adopter ITP professor tom igoe at NYU.
banzi had just been hired to teach new practices in interaction design at IDII, itself a research and innovation initiative of olivetti/telecom. at the time, he like many other physical computing enthusiasts made use of parallax’s basic stamp microcontroller, but the device cost about $100 and was very limited in memory, as well as requiring knowledge of the basic programming language.
the site of the former interaction design institute ivrea, where arduino was first developed
image © designboom
influenced by ben fry and casey reas‘s processing programming environment, which simplified coding and permitted the creation of stunning interactive and generative screen-based projects, banzi alongside his collaborators at IDII sought to create an accessible, relatively simple to learn, cross-platform device for the field of physical computing. they also wanted it to be affordable, in the range of $30. as students and faculty developed the project, the impending closing of the IDII encouraged banzi to launch the project as opensource under creative commons licensure, and to make his students the first beta testers of the concept. the semester was successful, and word about arduino spread quickly among colleagues and online, where the arduino community still thrives and grows today.
arduino takes its name from the former ‘bar di re arduino’ in this piazza in ivrea
image ©designboom
detouring into town, we visit the bar from which the family of microcontrollers takes its name. the ‘bar di re arduino’ is now under different management and is called ‘movida’, but davide assures us that it’s this place that was the local watering hole of founder massimo banzi while a professor at the interaction design institute ivrea. and when arduino existed as a prototype and business plan but still without a name, it was over drinks one night that the team, as the story goes, decided what their creation would be called.
there’s more behind that name, though: born in what is now ivrea, arduino of pombia was chosen king of italy from 1002 to 1014, and is popularly romanticized as a dedicated nationalist who sought to free his country from decades of foreign domination under the rule of the german ottonian dynasty. the revolutionary figure is a fitting namesake for the hardware producers, whose steadfast championing of opensource systems and alternative business models is a vital artery in the maker movement; and king arduino’s election from outside of the traditionally recognized noble lineage (albeit by a very limited sense of public) already parallels arduino’s democratization of programming and engineering.
WATCH: arduino’s davide gomba reflects on makerspaces and what they’ll mean for the future of factories
video © designboom
what’s next for the pioneering company? arduino has just recently launched scuola.arduino.cc, an integrated web portal that provides tutorials and project ideas from both company employees and the global arduino community, augmenting the already rich online community of diy hardware enthusiasts and arduino developers. arduino scuola addresses the international nature of its participants by providing information translated in english, italian, and german langauges. in real space as well, 2013 has seen the opening of an officina in malmo, focusing largely on educational initiatives (and where david cuartielles developed the arduino robot), as well as in bangalore, india.
the five members of the core team continue to collaborate from careers in new york and boston and lugano, switzerland, amidst their international travels for educational and cultural initiatives. the torino officina remains the heart of arduino’s infrastructure, but the company hopes to open more offices to expand their efforts in content creation and developmental projects.
as we catch our train out of turin, we’re struck by the way arduino’s factories and officine serve as striking microcosms of the company’s own ethos: the way man works in synergy with machine on arduino’s production lines; the italian attention to detail in aesthetics and quality control coupled with the heavy industrial heritage of turin and ivrea; arduino’s emphasis on education and outreach ventures; even the company’s partnering with an ecology of factories rather than adopting a conventional vertical, top-down approach. arduino and the very concept of opensource hardware is one of the sparks that ignited the maker movement, and the world that these makers are already constructing is one where sensors, microcontrollers, and smart systems– many themselves likely powered by arduino– might help us to live more efficiently, comfortably, and creatively within our environment. while integral to the heralded ‘new economy’, whats being created is something more than that: it’s a new ecology, a conceptual framework of collaboration whether between people and technology, among one another, or with their environments. and it’s happening at home, whether that means ‘made in italy’ in the factories that surround the birthplace of arduino, or built and shared and shaped and adapted in one of a thousand cities by any of many thousand people throughout the world.
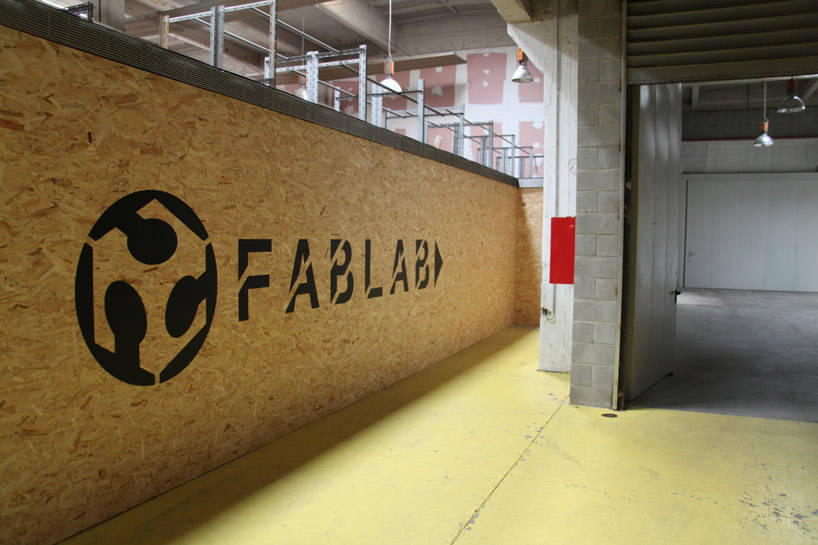
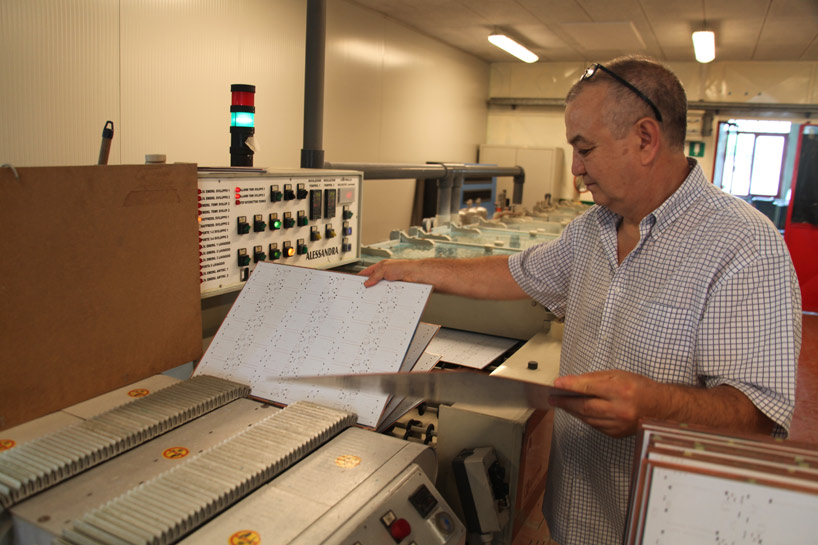
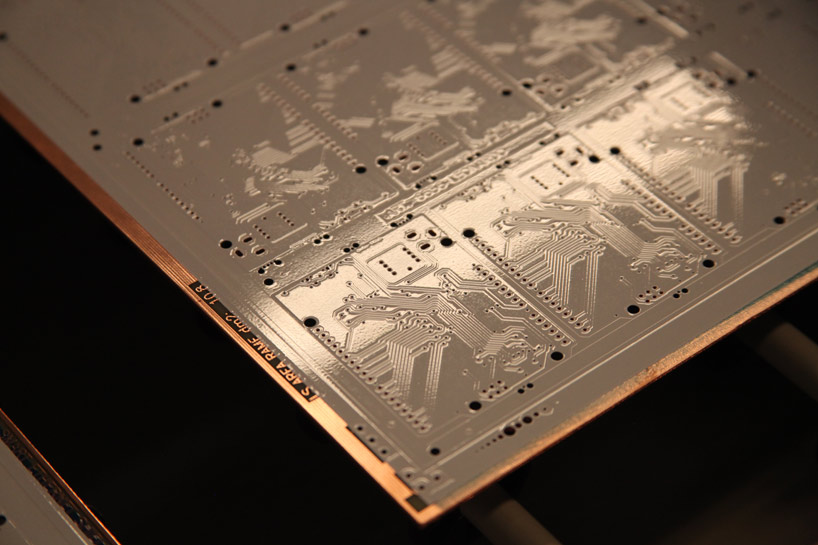
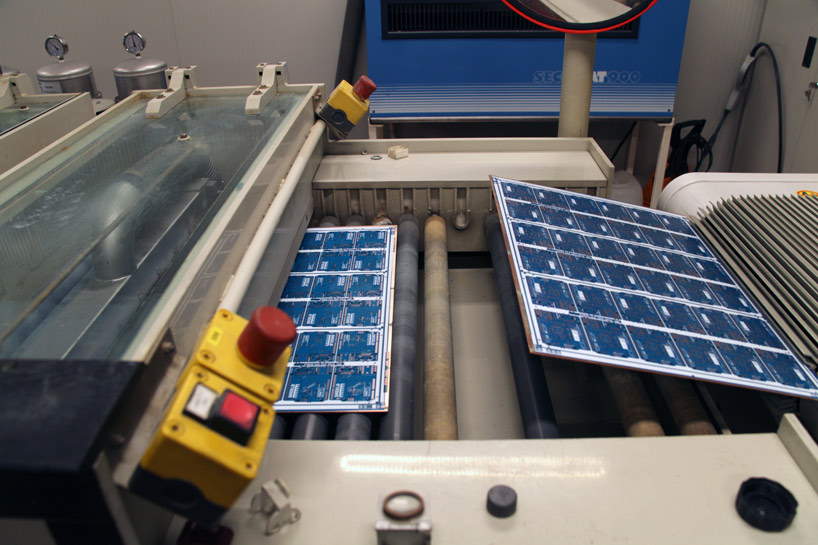
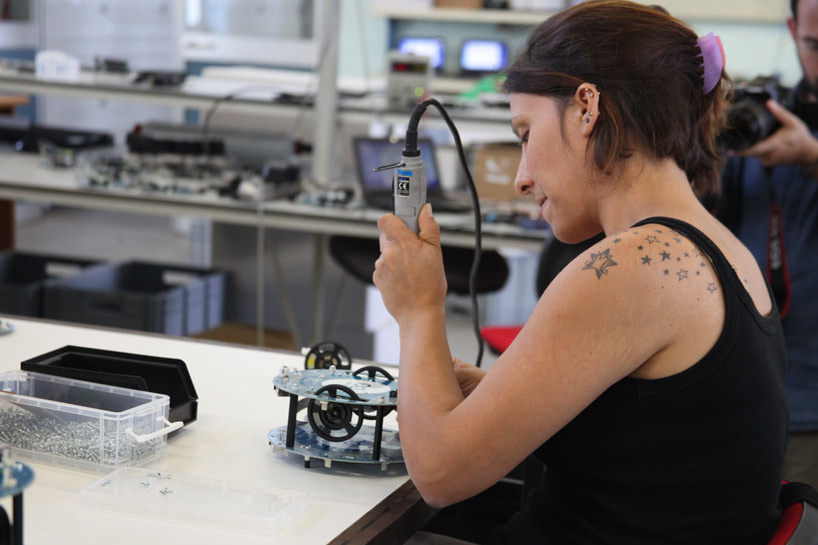
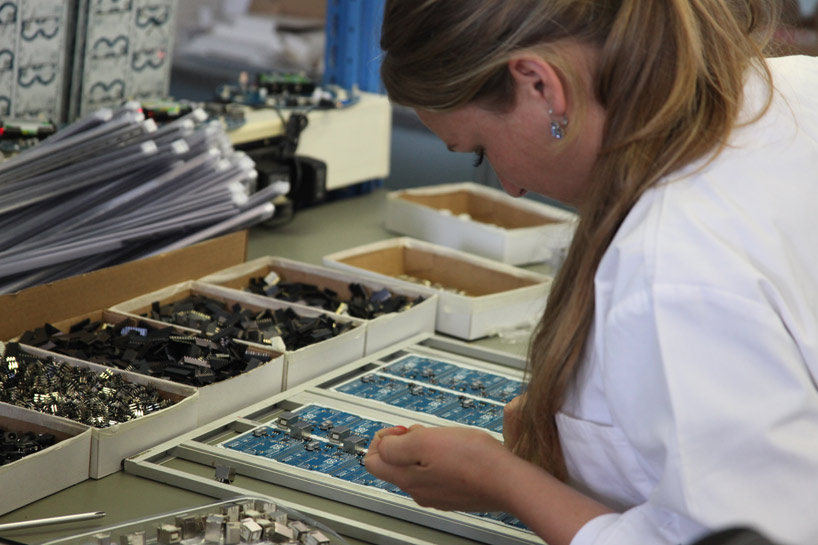
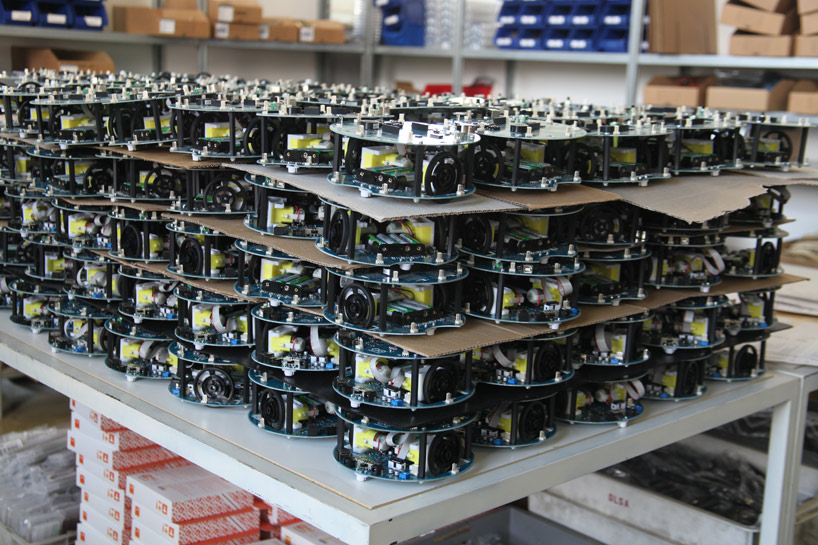
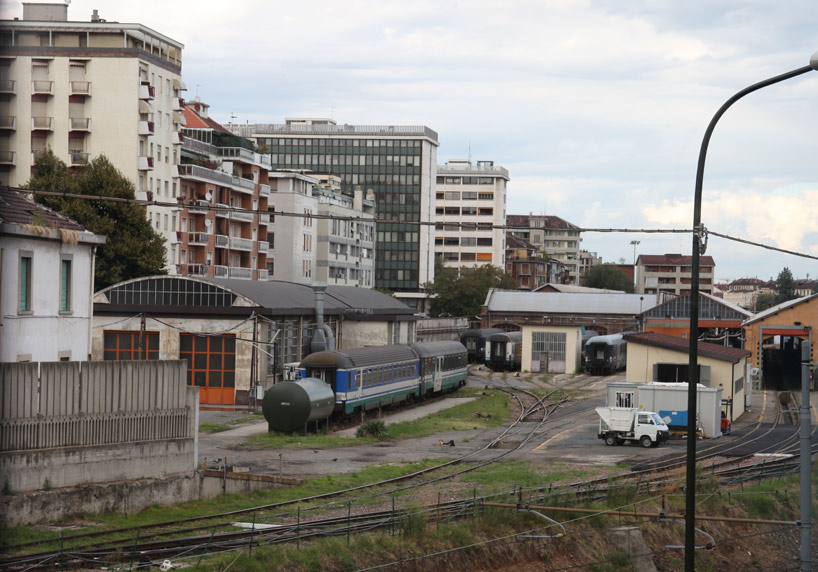
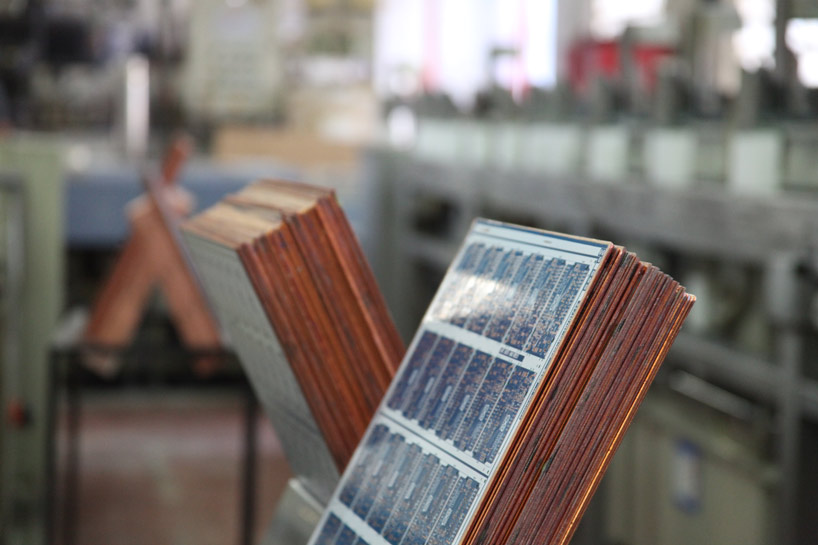
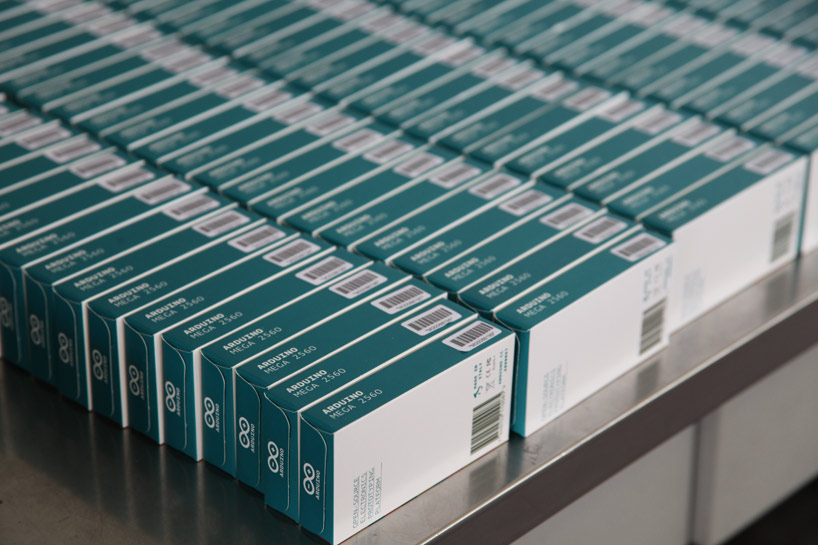
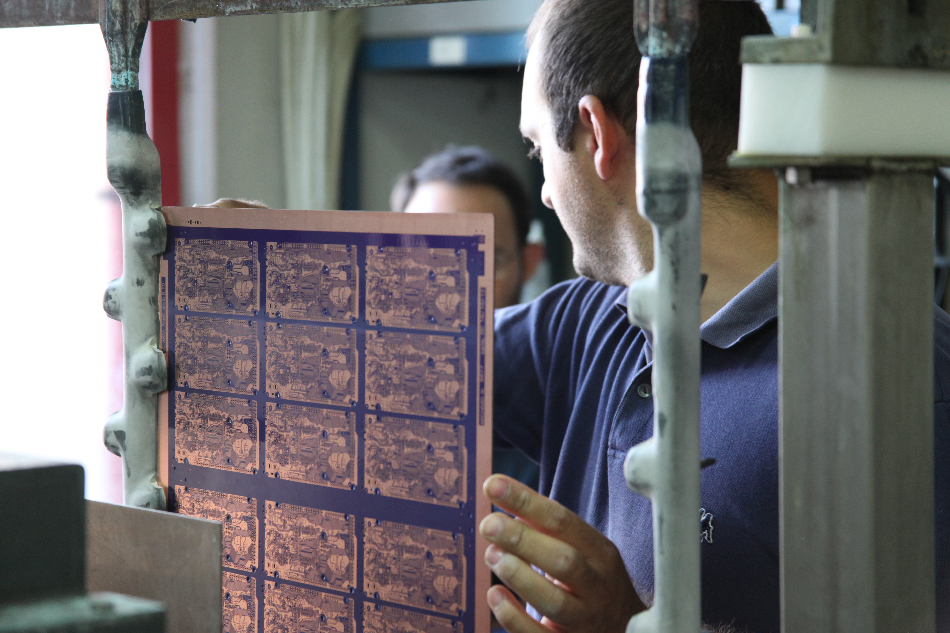
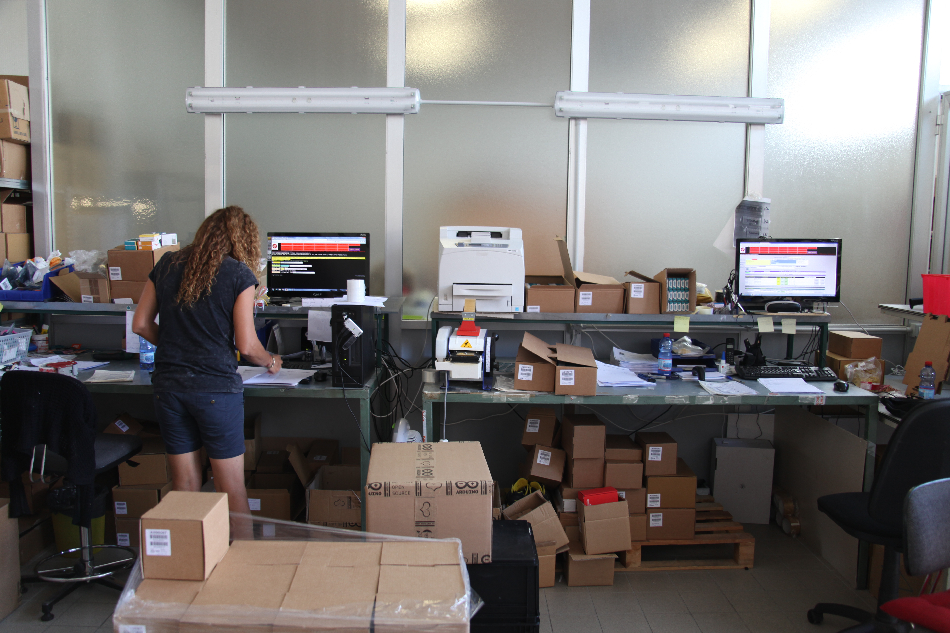